Waste to Worth: Ethiopian Company Eyes GENMAX Foam Recycling
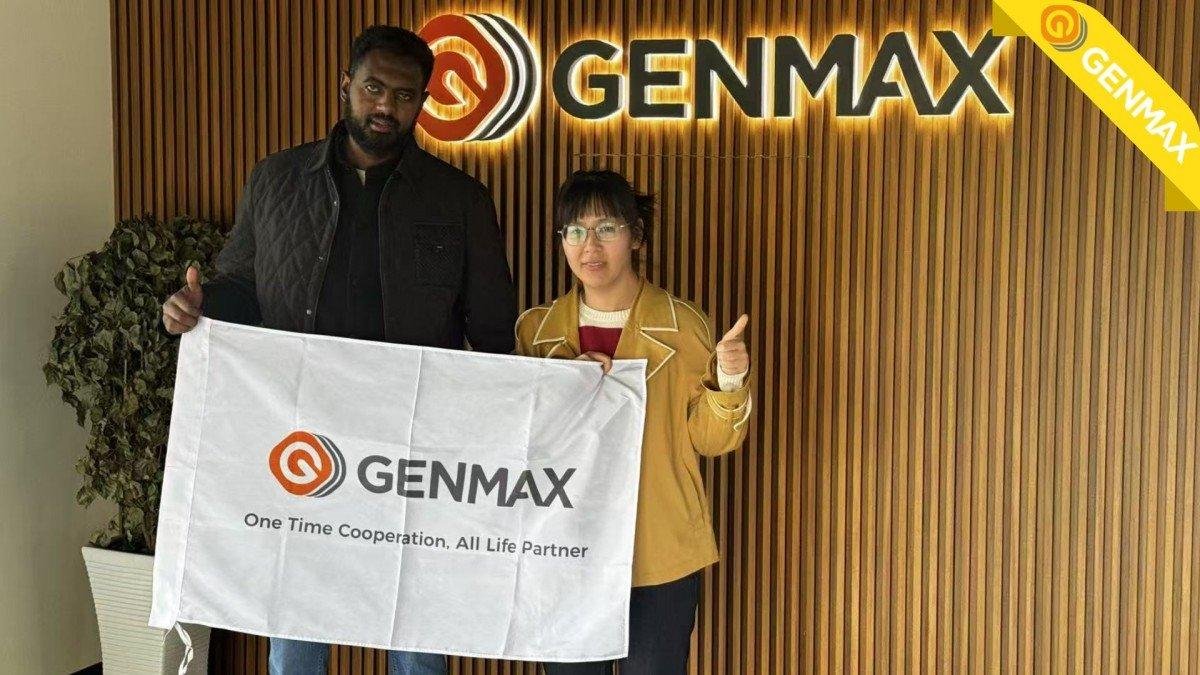
A small group of business owners from Ethiopia visited us last week to look at GENMAX rebonded foam machines. They plan to recycle foam waste in Addis Ababa. This practical method shows how Ethiopian businesses are discovering new opportunities.
Solving a Local Problem
“We see foam waste everywhere in Addis,” said the company owner during our meeting. “Furniture makers and mattress factories throw it away, but we think we can turn it into something valuable.”
This simple observation has led the group to explore foam recycling. As Ethiopia’s cities grow, so does furniture production – and with it, the amount of foam scraps that usually end up in landfills.
The Ethiopian visitors weren’t interested in fancy technology. They wanted practical equipment that could help them convert this waste into usable products.
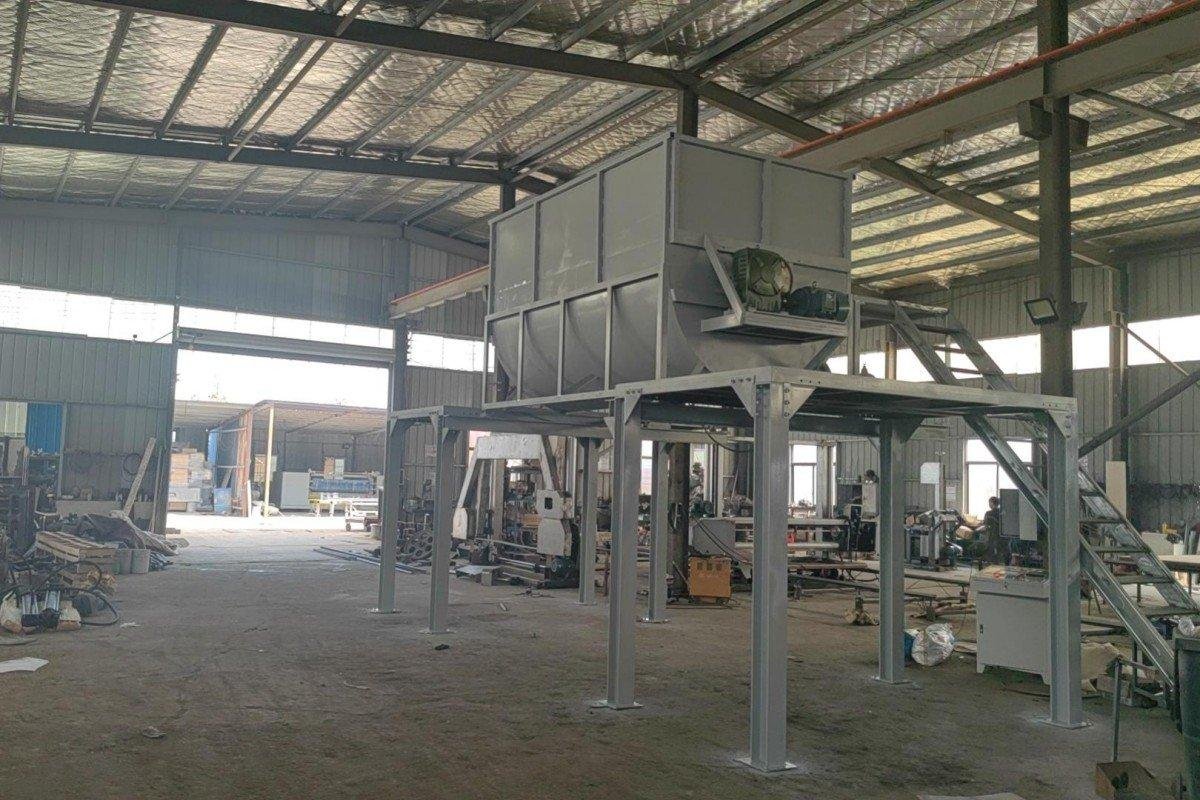
Matching the Machine to the Market
“Our power sometimes goes out,” the operations manager said, glancing at various GENMAX models. “We need something reliable that can handle these conditions.”
The group had a clear list of practical concerns:
- Equipment that works with basic infrastructure
- Machines simple enough for workers to learn quickly
- Systems that can process different qualities of foam waste
- Output that meets the needs of local builders and manufacturers
They asked clear questions about maintenance needs. They also wanted to know how to keep the machine running if parts need to be replaced.
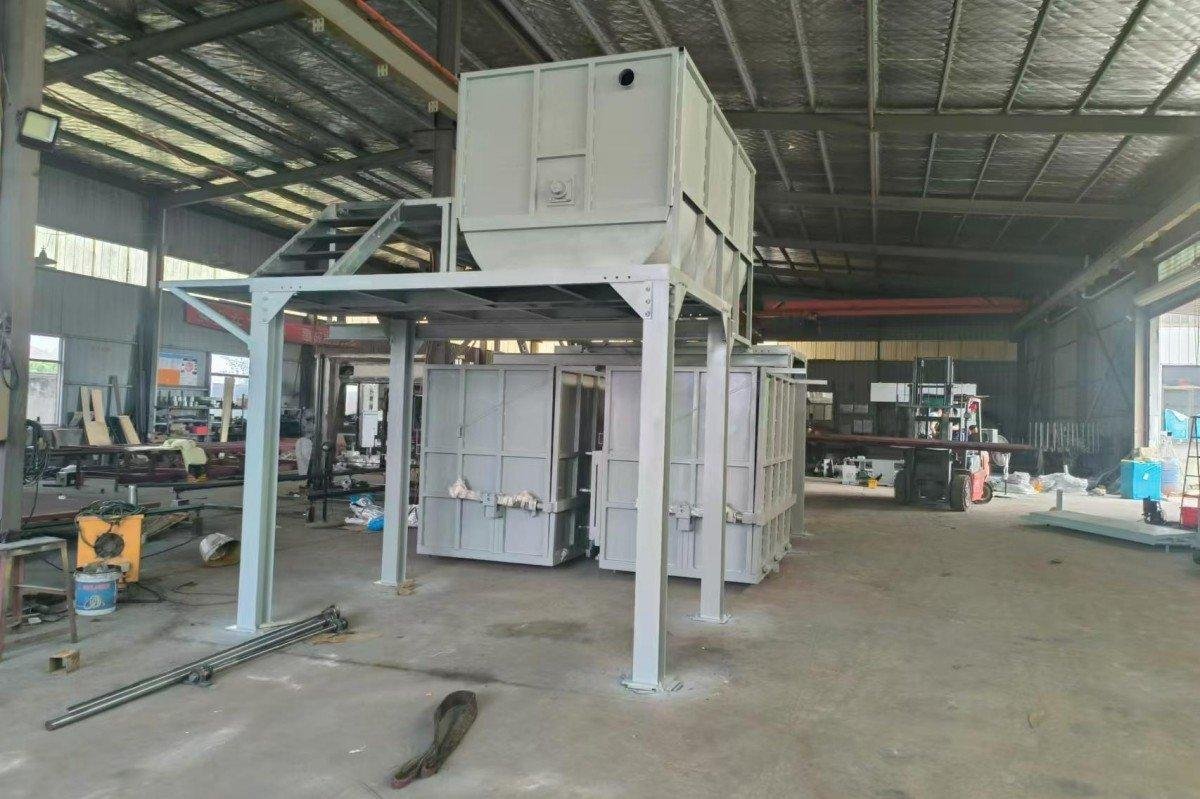
Ready-Made Customers
What impressed me most was that the Ethiopian team had already lined up potential customers before buying any equipment.
“Construction companies in Addis need affordable insulation,” the business owner told us. “They’re ready to try our recycled foam if we can make it at the right price.”
The team also brought sample requirements from these customers. These were simple specs for density and fire safety that their products must meet.
“We’re starting with products we know we can sell,” said the sales manager. “Nothing fancy, just practical materials that local businesses need.”
Collecting the Raw Materials
The Ethiopian team has also worked out how they’ll get the foam waste they need. They’ve already talked to furniture makers and mattress factories about collecting their scraps.
“We can get enough material to start production right away,” explained their logistics person. “We’ve already arranged collection from the biggest factories in Addis.”
This practical way of securing their supply chain shows why small businesses in Ethiopia often succeed. They build relationships and solve problems one step at a time.
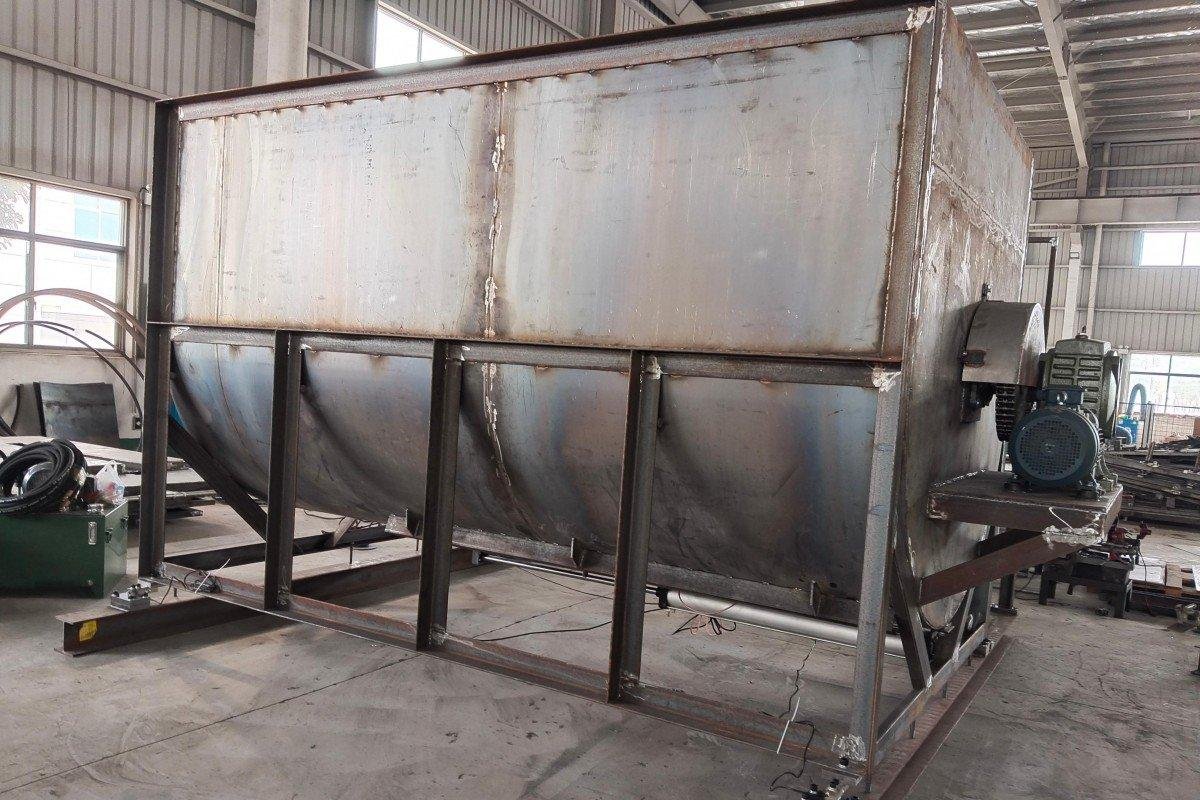
Learning the Business
The Ethiopian visitors focused on the basic production process during our equipment demos, not the technical details.
“We need to know how to make consistent products from different types of foam waste,” said the operations manager. “This is new for Ethiopia, so we need to learn the fundamentals.”
They asked for training materials in simple language and wanted to know if video tutorials were available for their workers to watch.
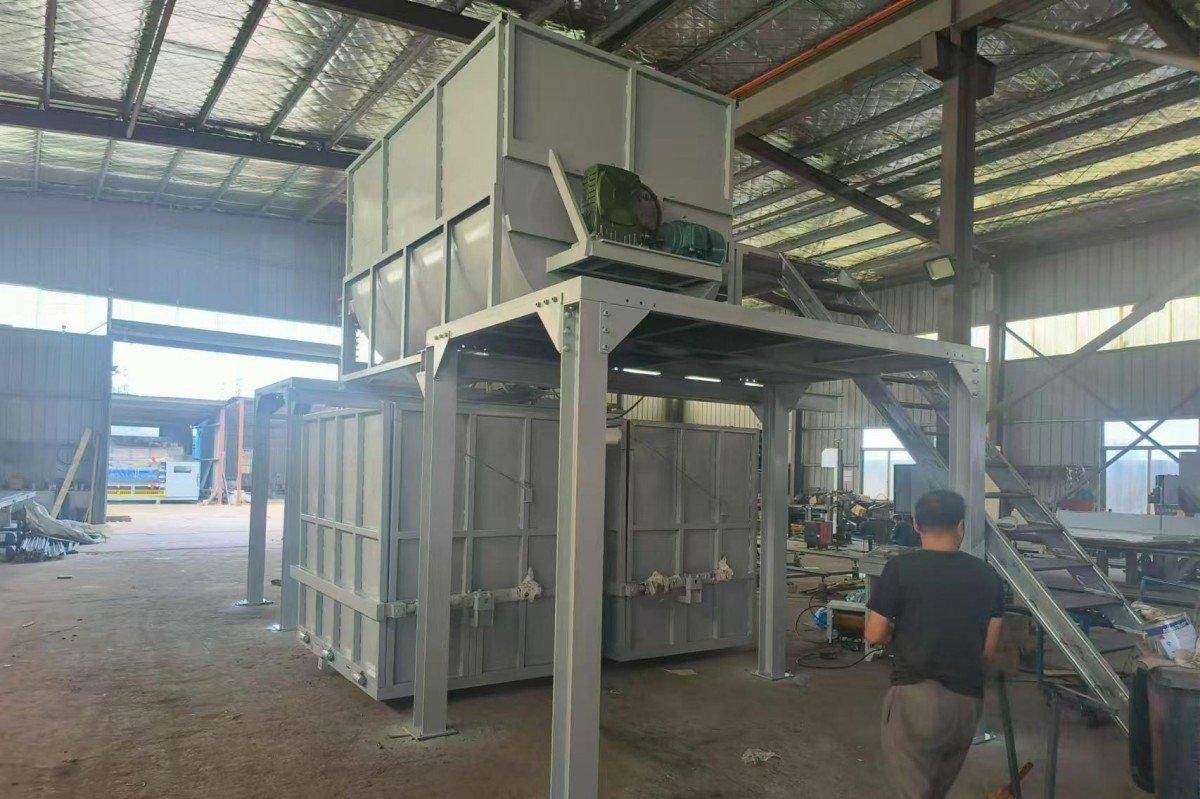
Starting Something New
At the end of our meeting, it was obvious that these Ethiopian entrepreneurs were smartly and practically seizing a business opportunity that suits their country.
“We’re not trying to do anything complicated,” the owner summarized. “Just turning waste that’s a problem into products people need, while creating jobs.”
The group will continue evaluating the GENMAX equipment as part of their business planning. Ethiopian businesses are finding ways to combine environmental benefits with smart business practices. Their simple approach highlights these opportunities.