Thai Mattress Factory’s Packing Success with GENMAX Machines
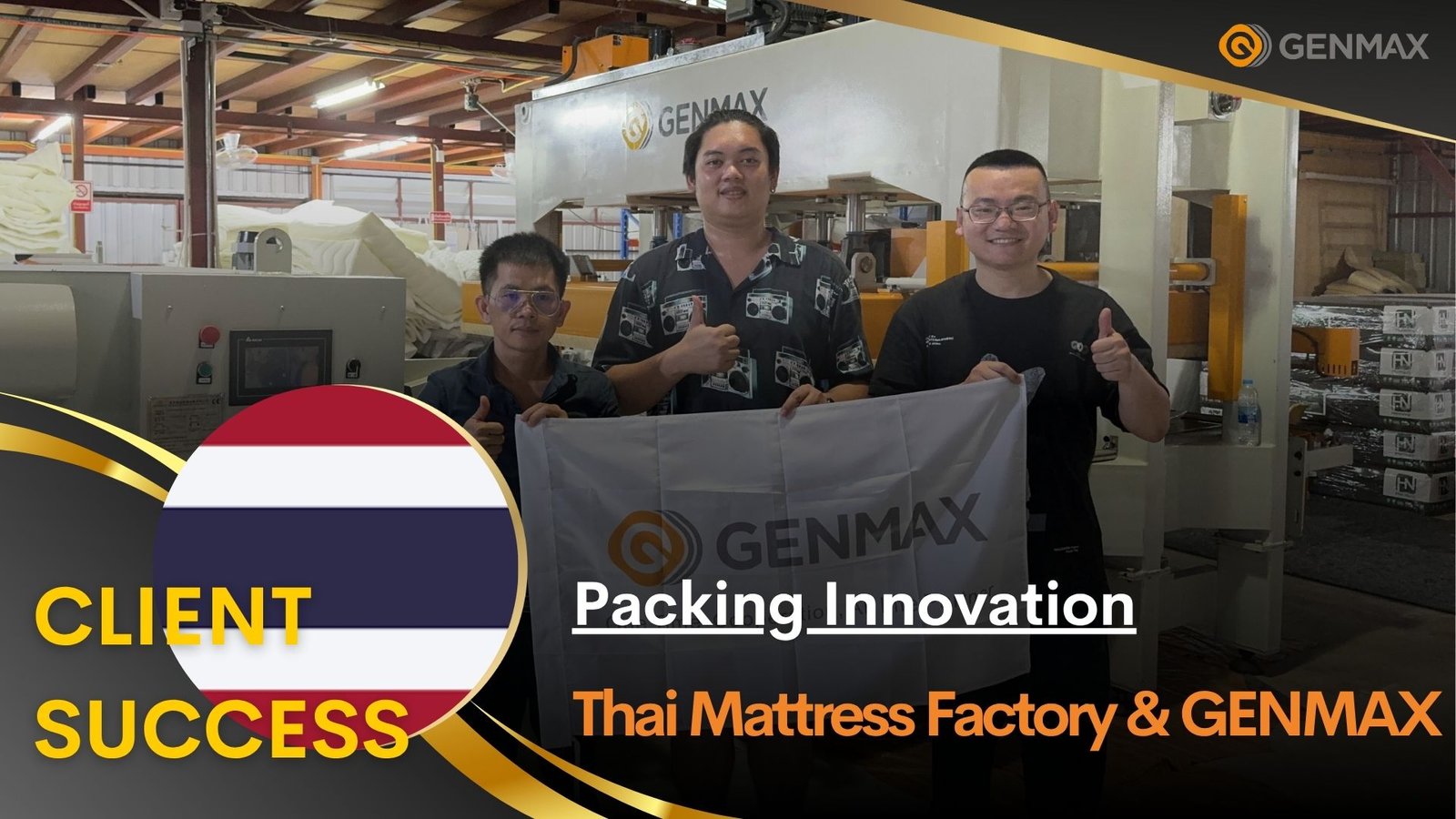
Ever feel like your mattress packing slows down your whole production line? Or that bulky mattresses are eating up your storage and shipping costs? If you’re running a mattress factory, these problems hit close to home.
That’s exactly what a client in Thailand was dealing with.
They wanted a quicker, smarter way to roll, pack, and compress mattresses. They also needed to keep quality and flexibility intact.
GENMAX enhanced their packing process with two machines: the MJB Mattress Rolling and Packing Machine, and the ZYSJ Vacuum Packing Machine.
Packing Challenges Held Them Back
- Slow manual rolling and packing that slowed down production
- Trouble handling different mattress types: foam, latex, memory foam, toppers
- Bulky mattress sizes taking up too much storage and transport space
- Needed flexible packing modes to meet different customer demands
Sound familiar? If you’ve seen this in your factory, keep reading.
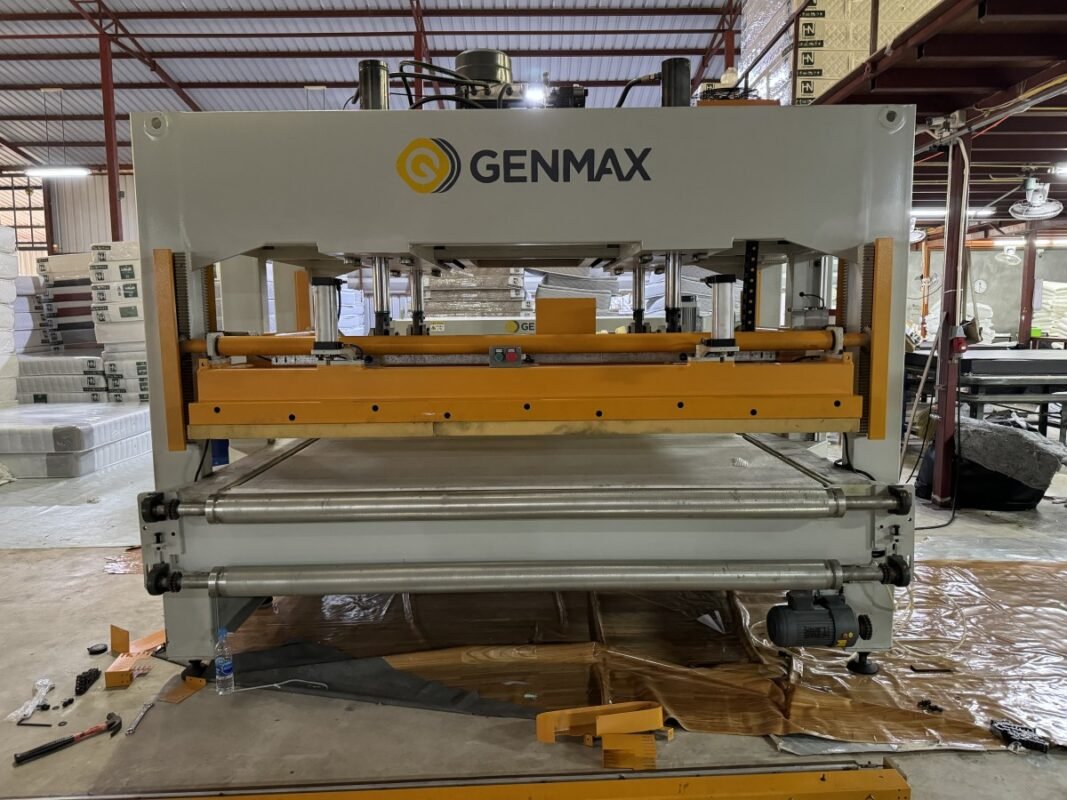
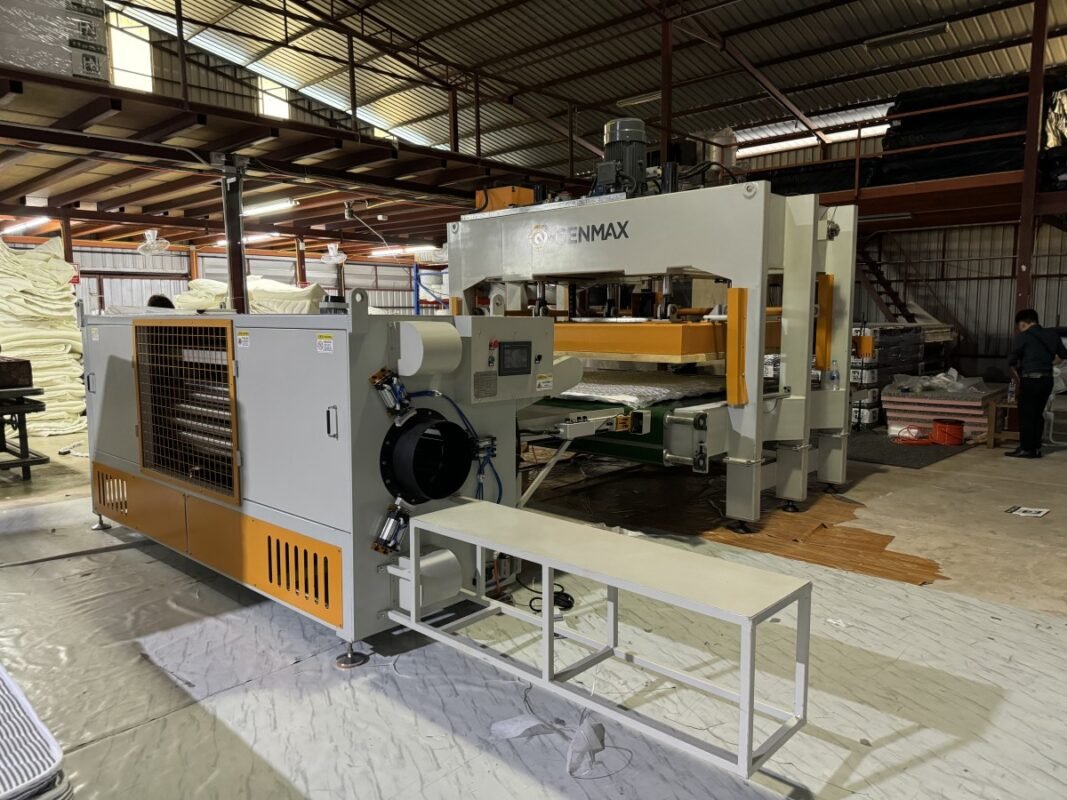

The GENMAX Machines That Made the Difference
MJB Mattress Rolling and Packing Machine
- Rolls light to medium mattresses, toppers, ped beds, and wedges. No compression unit is needed.
- Offers three feeding modes: Pre-bagging with a long tail rolled and sealed on the mattress./Pre-bagging plus rolling extra PE/stretch film./No pre-bagging, just rolling extra PE/stretch film.
- Handles folded toppers and foam types — foam, latex, memory foam
- Hydraulic Roll Diameter Adjustment System for smooth, consistent rolling
- Oscillating stretch film carrier covers all mattress sizes with one film width
ZYSJ Vacuum Packing Machine
- Compresses spring, foam, and memory foam mattresses with vacuum and heat sealing
- Uses an electronic control system for reliable, consistent packing
- Cuts mattress volume up to 40%, saving storage and transport space
- Automates vacuuming and sealing, speeding up packing and cutting labor costs
Packing Speed and Space: The Gains
We didn’t just ship machines and walk away. We worked side by side with the factory from start to finish.
Here’s what made the difference:
- Quick, clear communication: We responded to questions in under 24 hours, so the client always got answers right away.
- Custom packing solutions: Our team designs setups for your production needs. They’re ready in just 3 days.
- Smooth project management: We tracked every step — from specs to installation and training — so nothing got missed.
- Industry know-how: We have 15 years of experience in mattress machinery. We understand what factories need to run smoothly.
- Global experience, local focus: We’ve worked with over 5,000 clients worldwide. So, we tailor solutions to meet local standards and challenges.
- End-to-end supply chain support: From sourcing to delivery, we optimize costs and timing to keep production flowing.
- On-the-ground after-sales: Our service centers and local tech teams mean that help is always close by.
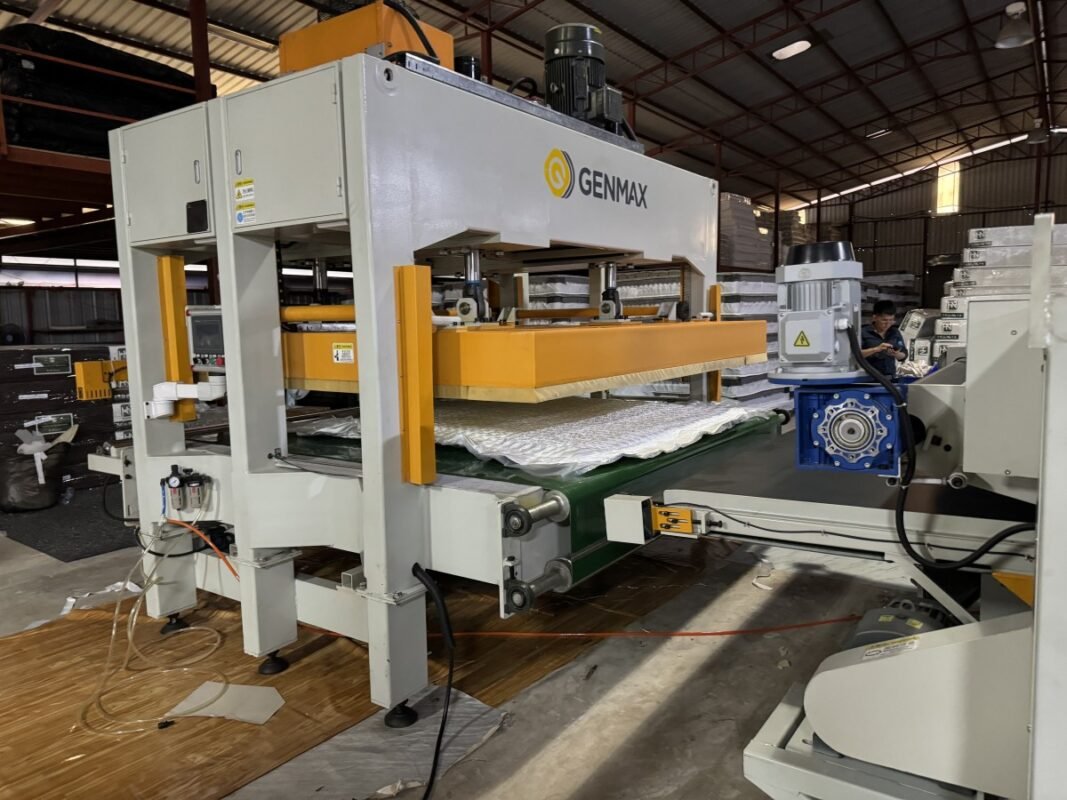

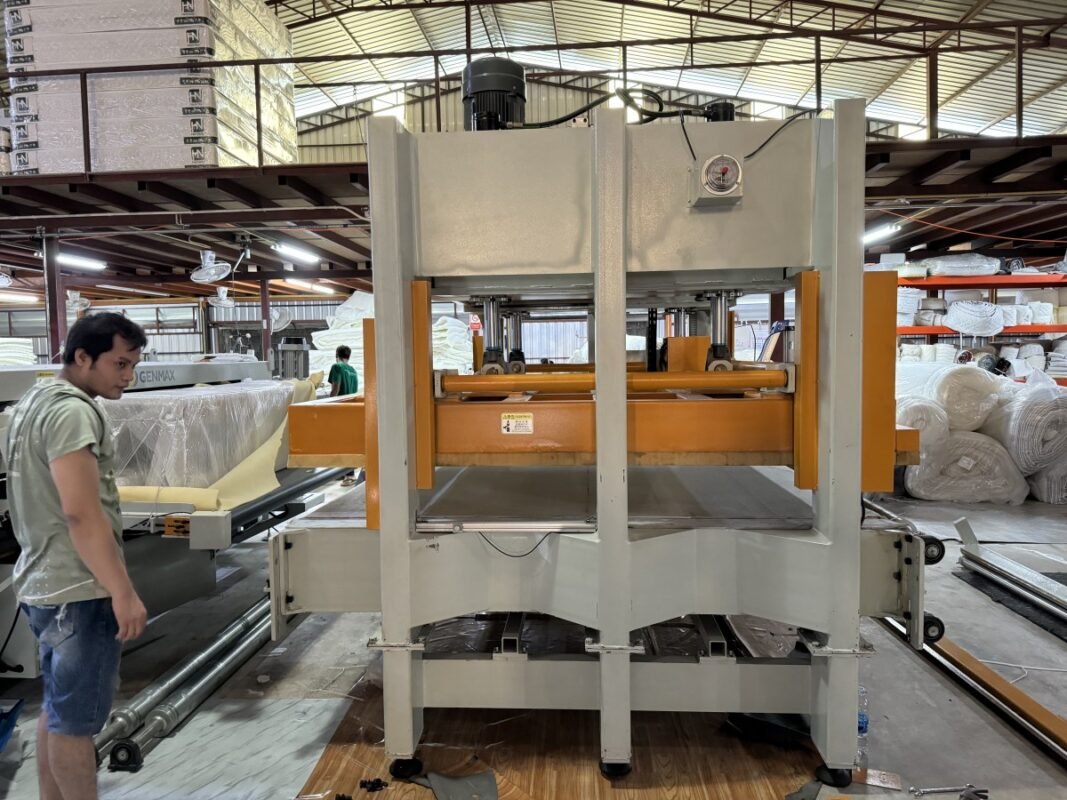
What This Means for Your Factory
If your packing line is a bottleneck or storage costs are cutting into profits, consider this:
- Pick machines that handle your full range of mattress types — foam, latex, springs — without extra fuss.
- Choose packing solutions with flexible feeding modes so you can switch between products easily.
- Work with suppliers who offer fast response times and local support to avoid costly downtime.
- Connect your packing machines to a supply chain system. This helps keep costs low and quality steady.
- Partner with companies that track your project fully, from order to installation and beyond.
Buying Smart: What Mattress Factories Should Watch Out For
When investing in rolling and vacuum packing machines, focus on these factory-critical points:
- Compatibility: Will the machine handle your mattress types and sizes?
- Flexibility: Can it switch feeding modes quickly to match your production schedule?
- Support: Is there a local team ready to solve problems fast?
- Installation: How quickly can the machine be up and running with minimal disruption?
- Cost Efficiency: Will it reduce labor, save space, and cut transport costs?
- Supply Chain Integration: Does the supplier offer end-to-end support from raw materials to delivery?
Avoid vendors who just sell machines without ongoing support. Your packing line is too critical to risk downtime.
Client Success Snapshot: Thailand Mattress Factory
Metric | Before GENMAX Machines | After Installation (3 Months) | Improvement |
Mattress packing speed | 25 mattresses/hour | 90 mattresses/hour | +60% |
Storage space used per batch | 100 cubic meters | 60 cubic meters | -40% |
Labor hours per 100 mattresses | 4 hours | 1 hours | -70% |
Packing error rate | 3% | 0.5% | -70% |
Performance Comparison: MJB vs. Traditional Rolling Machine
Feature | Traditional Rolling Machine | MJB Mattress Rolling Machine |
Compression Unit | Yes | No |
Mattress Types Supported | Limited foam only | Foam, latex, memory foam, toppers |
Feeding Modes | Single mode | Three flexible modes |
Roll Diameter Adjustment | Manual | Hydraulic system |
Film Coverage | Fixed width | Oscillating stretch film carrier |
Sources
International Sleep Products Association (ISPA), “Mattress Industry Trends 2024,” ispa.com
Thailand Board of Investment, “Manufacturing Sector Outlook 2025,” boi.go.th
If your Mattress Factory has slow packing, high labor costs, or bulky shipments, it’s time to rethink your packing line.
GENMAX Machines and support offer faster, cleaner, and cheaper packing. You’ll work with partners who truly understand the mattress business.
Ready to upgrade your packing line in Thailand or anywhere else? Let’s talk.