From Foam Waste to Value: Uzbekistan Factory’s Recycling Success with GENMAX
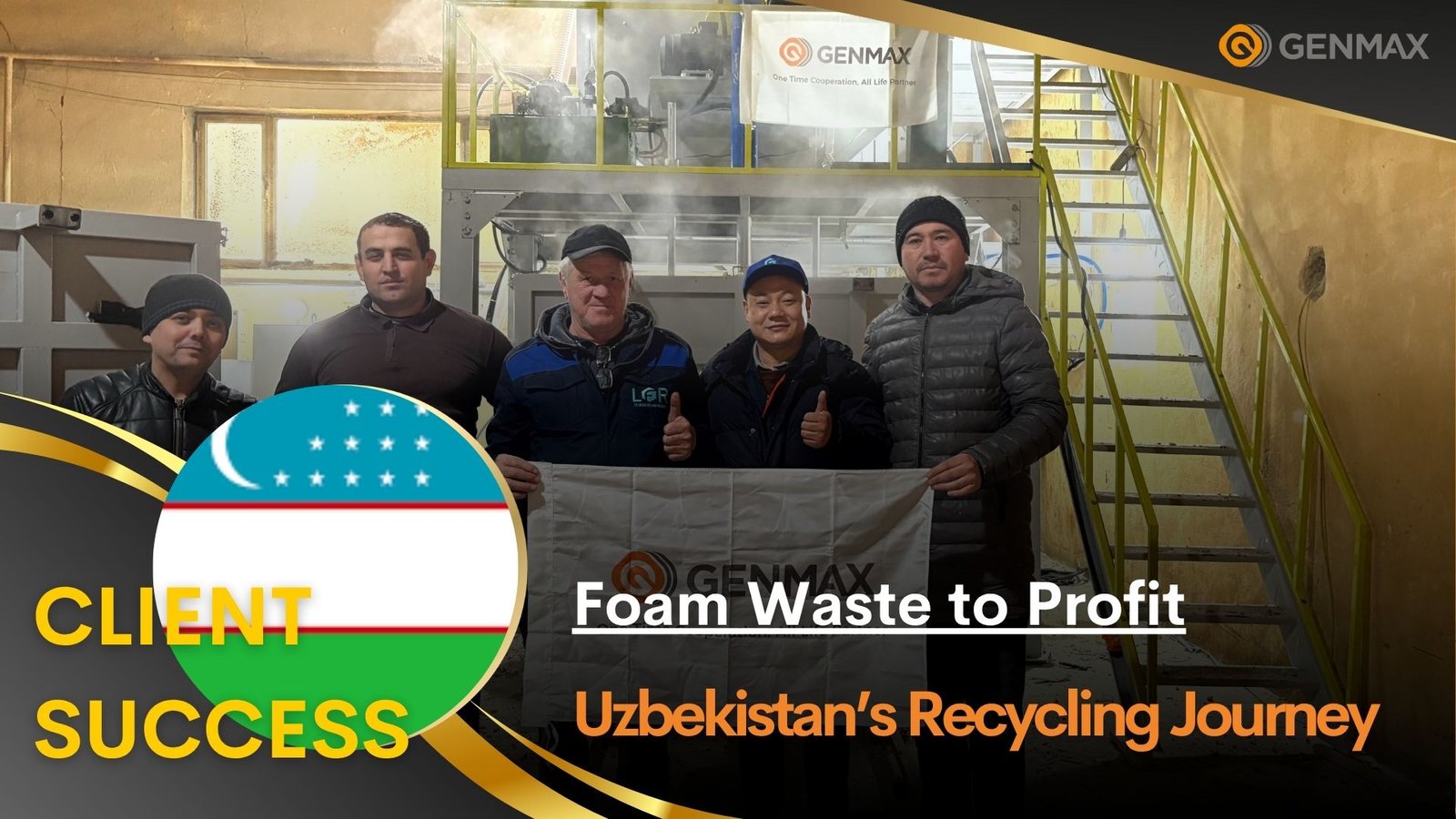
Foam waste piling up in your factory? Throwing it away only adds to costs and hurts your bottom line. What if you could recycle scrap foam into valuable products? You’d cut waste and save money too!
A mattress factory in Uzbekistan faced this exact challenge.
They needed a dependable and efficient way to process foam scraps. They aimed to turn these scraps into rebonded foam blocks. These blocks can be used for carpet underlay and gym mats.
GENMAX provided a custom solution with two main machines: the PS3878-PU Foam Crushing Machine and the RF02 Foam Rebonding Machine. This setup helped create a foam recycling line that changed their operations.
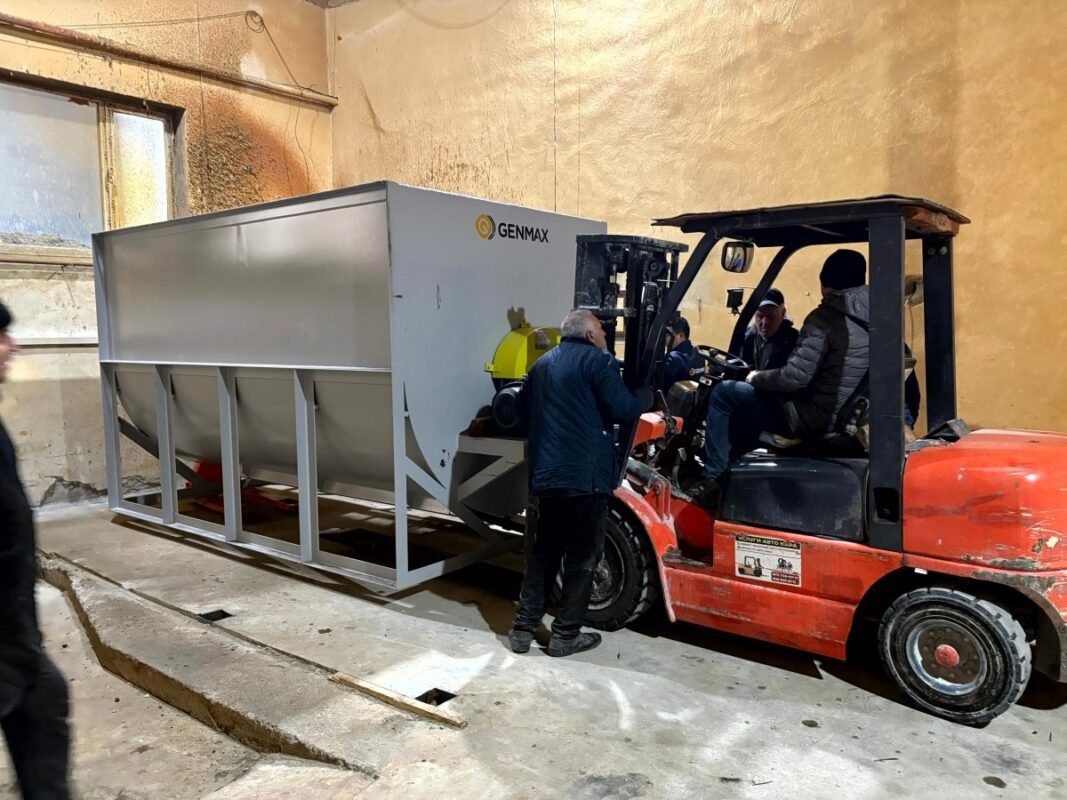
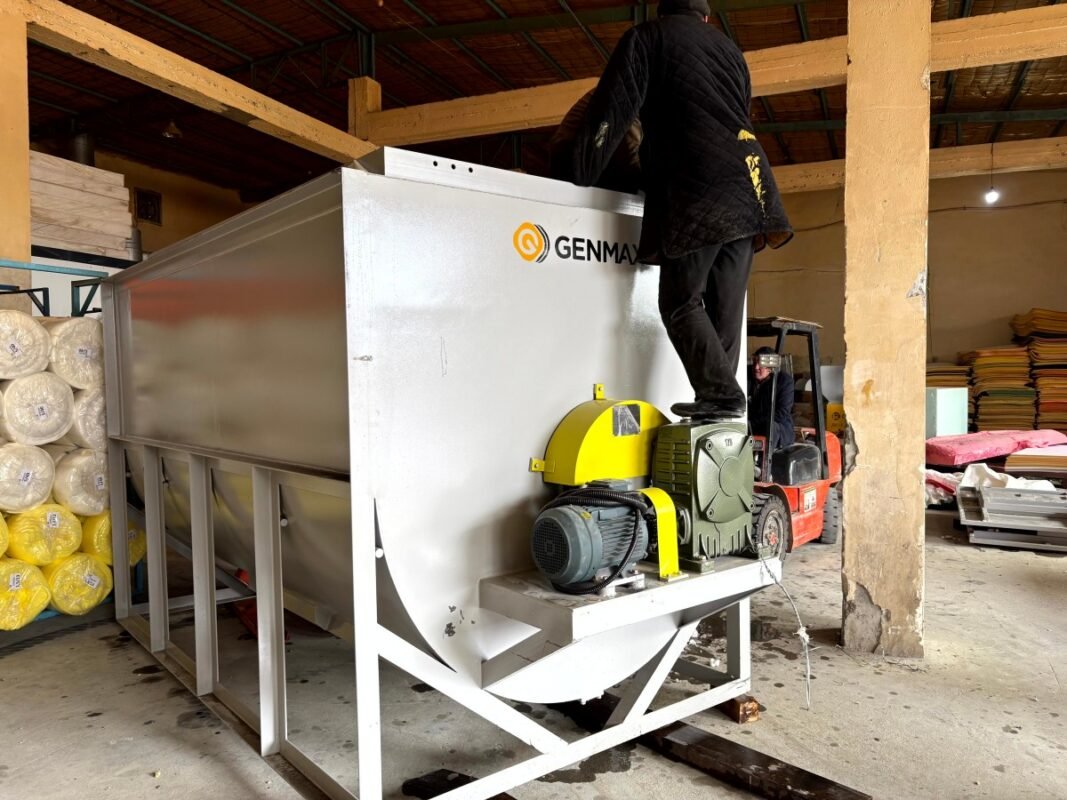
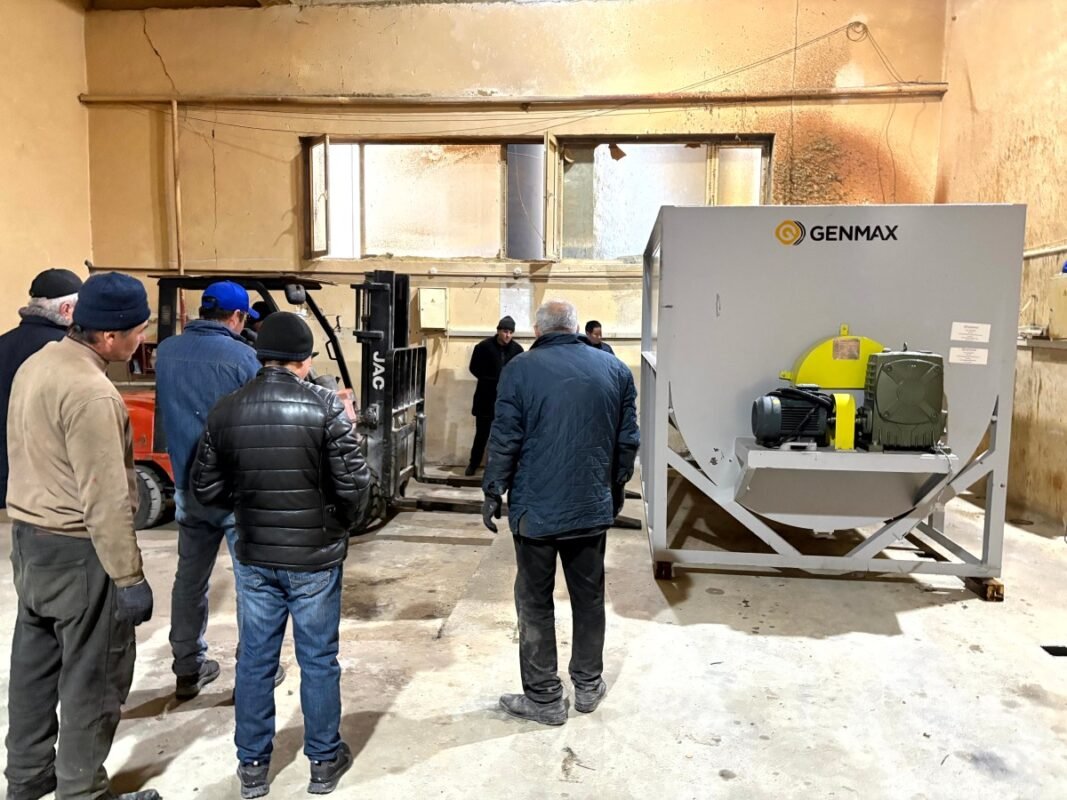
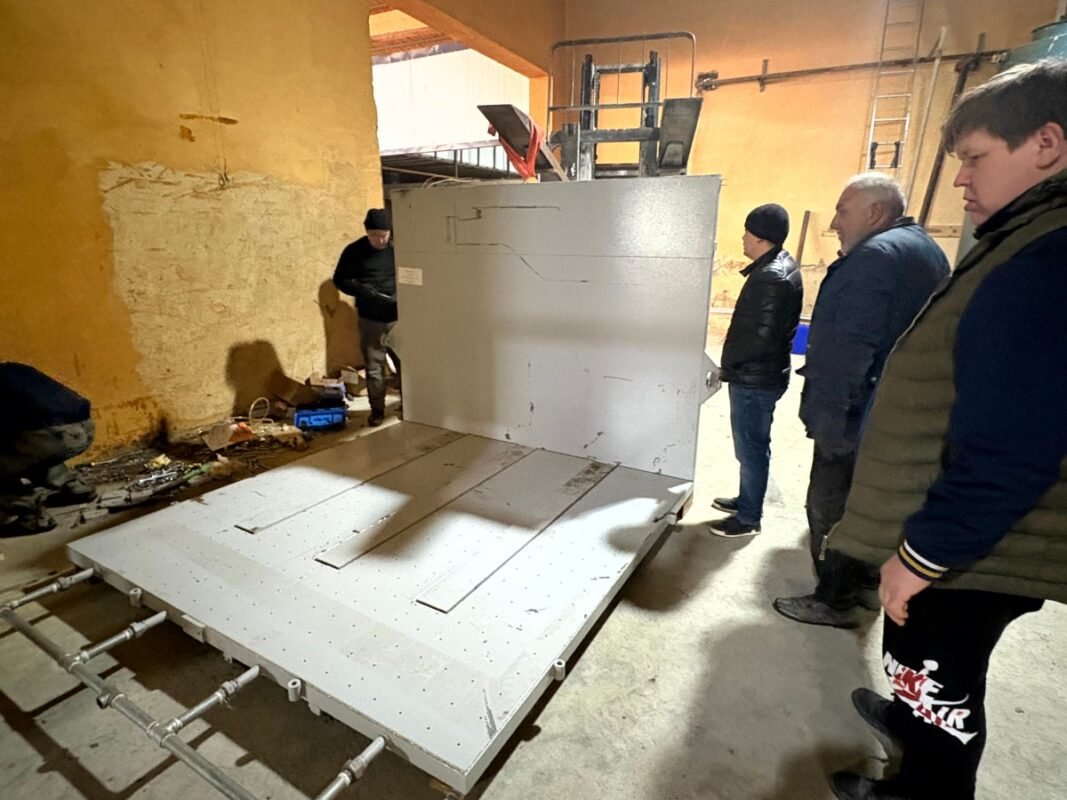
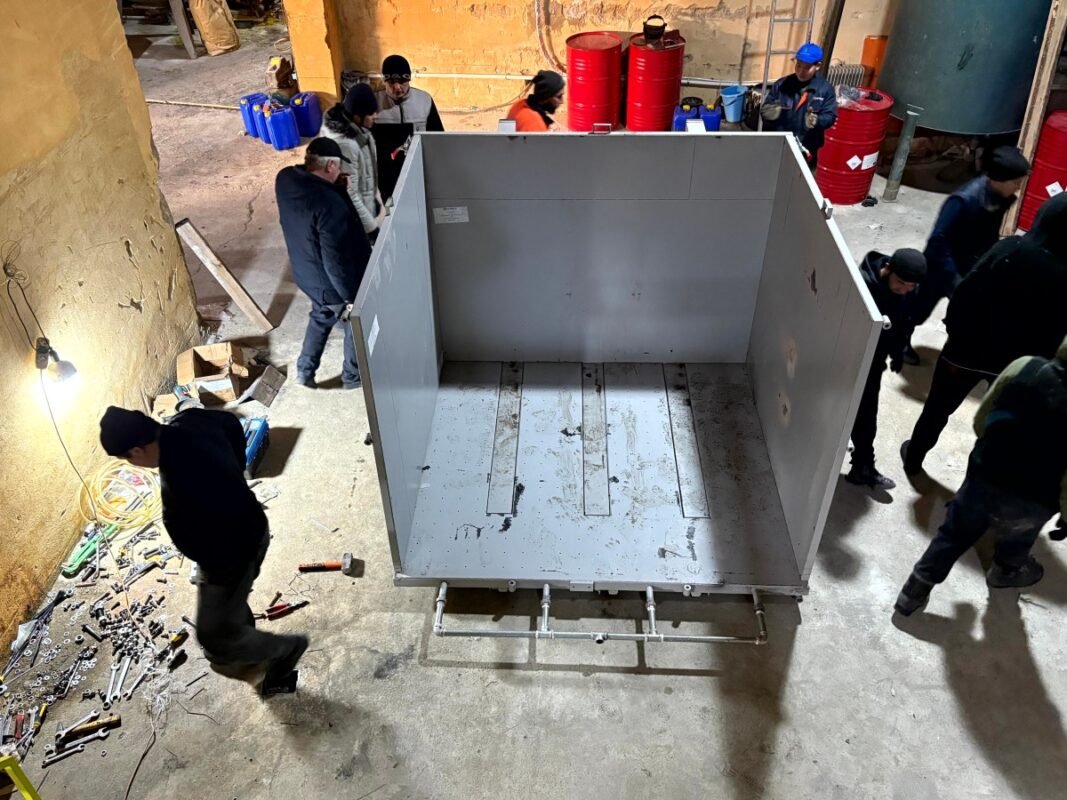
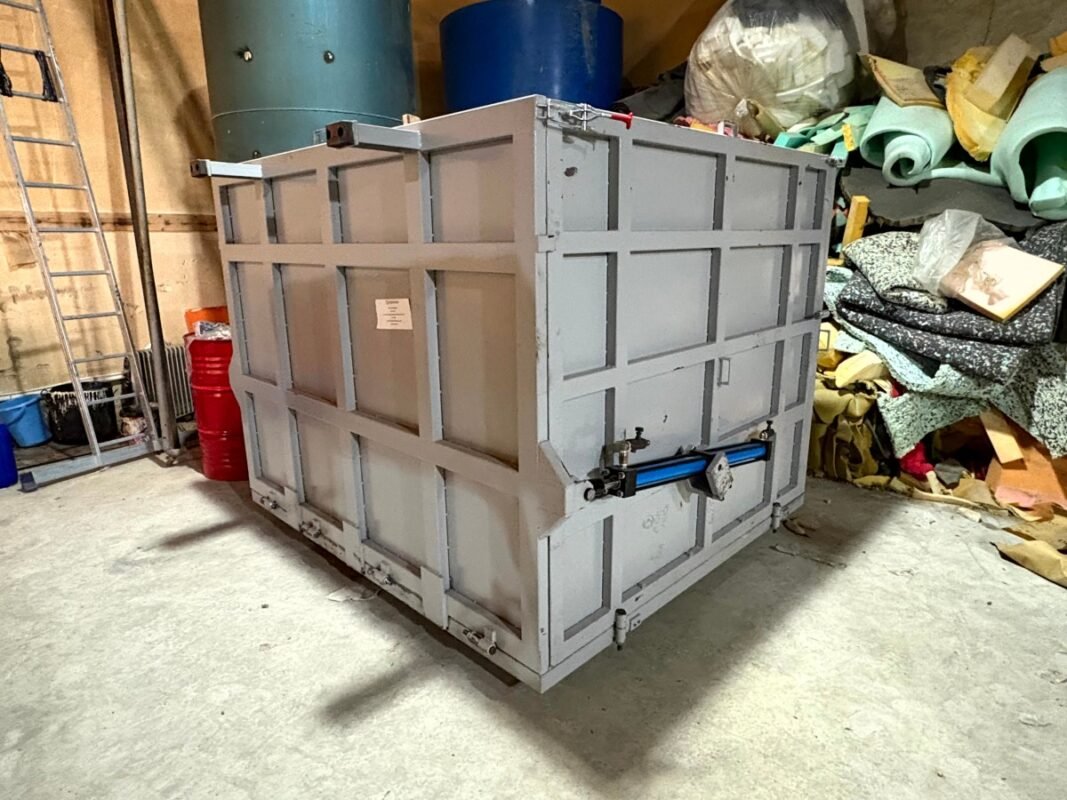
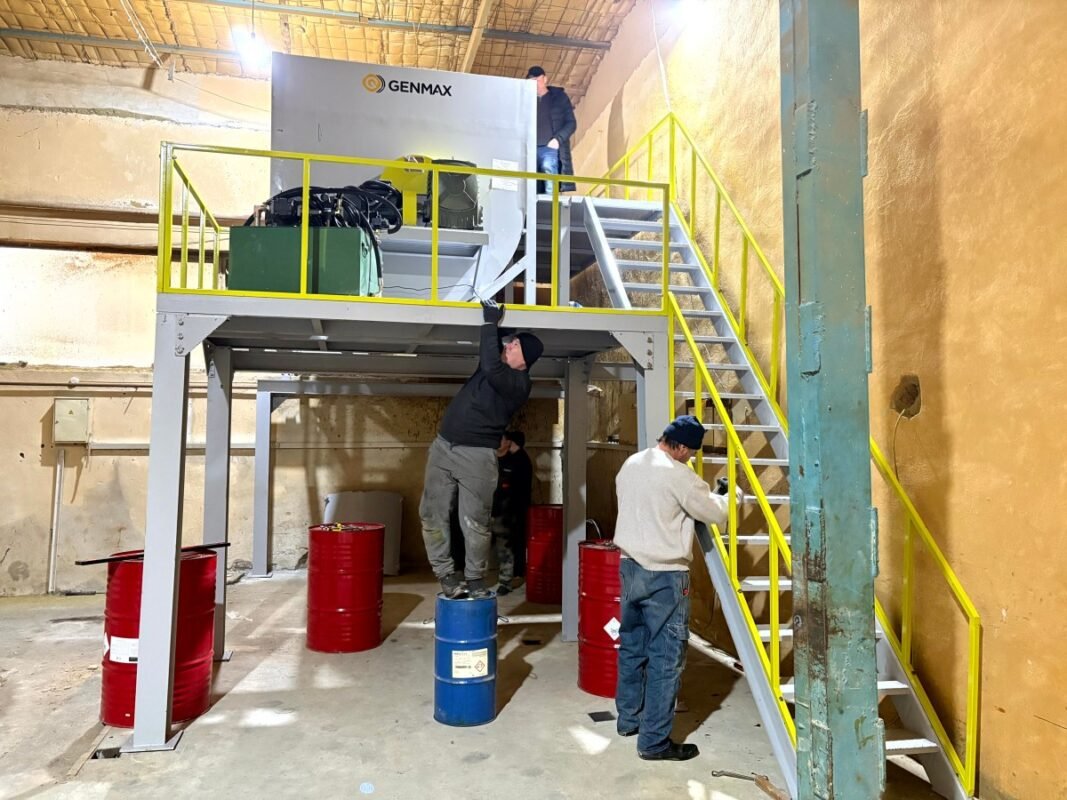

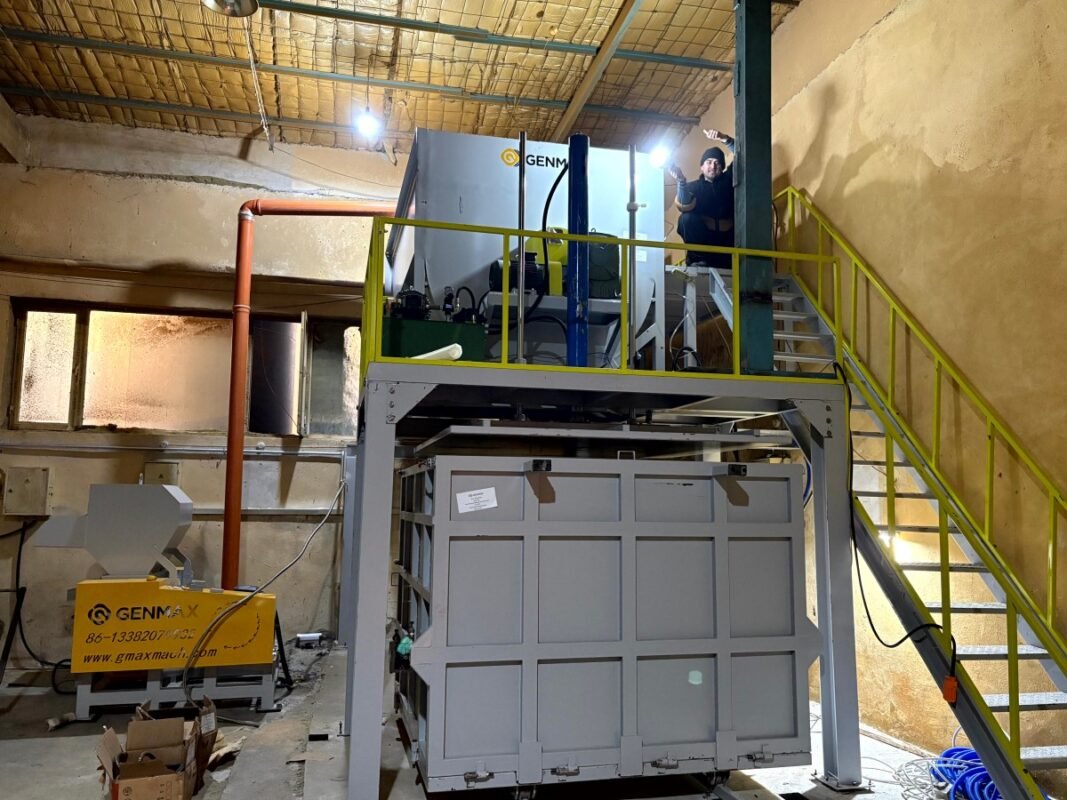
Foam Waste Was Draining Resources
- Foam scraps and cloth waste cluttered production areas
- No efficient system to reuse or recycle foam leftovers
- High costs from constantly buying new raw foam materials
- Needed a recycling line that could handle different foam densities and scrap types
If your factory struggles with foam scrap piling up, this story might spark some ideas.
GENMAX Machines Built for Efficient Foam Recycling
PS3878-PU Foam Crushing Machine
- Shred sponge scrap, cloth, and thrum waste into uniform granules
- Large feeding port and crushing port
- Output capacity of up to 1,000 kg/hour
- Four rows of fixed knives and three rows of rotary knives ensure thorough crushing
- Powerful 35.5 kW motor designed for continuous industrial use
- Compact footprint fits factory floors without hassle
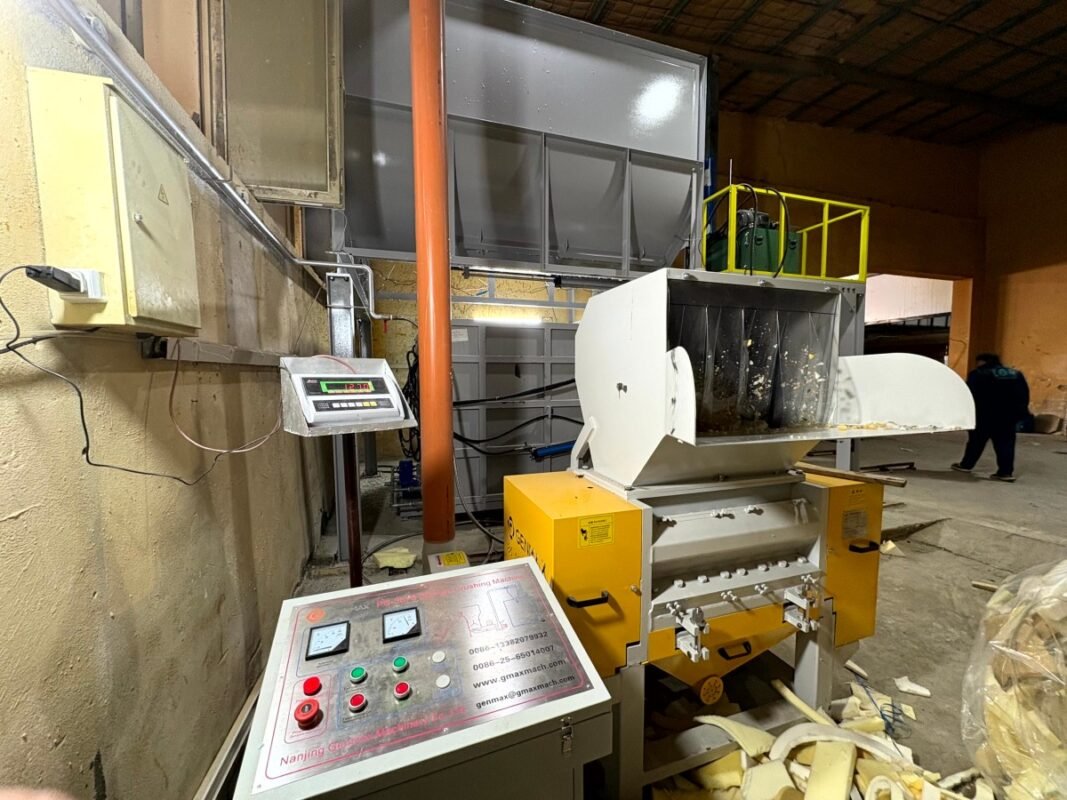
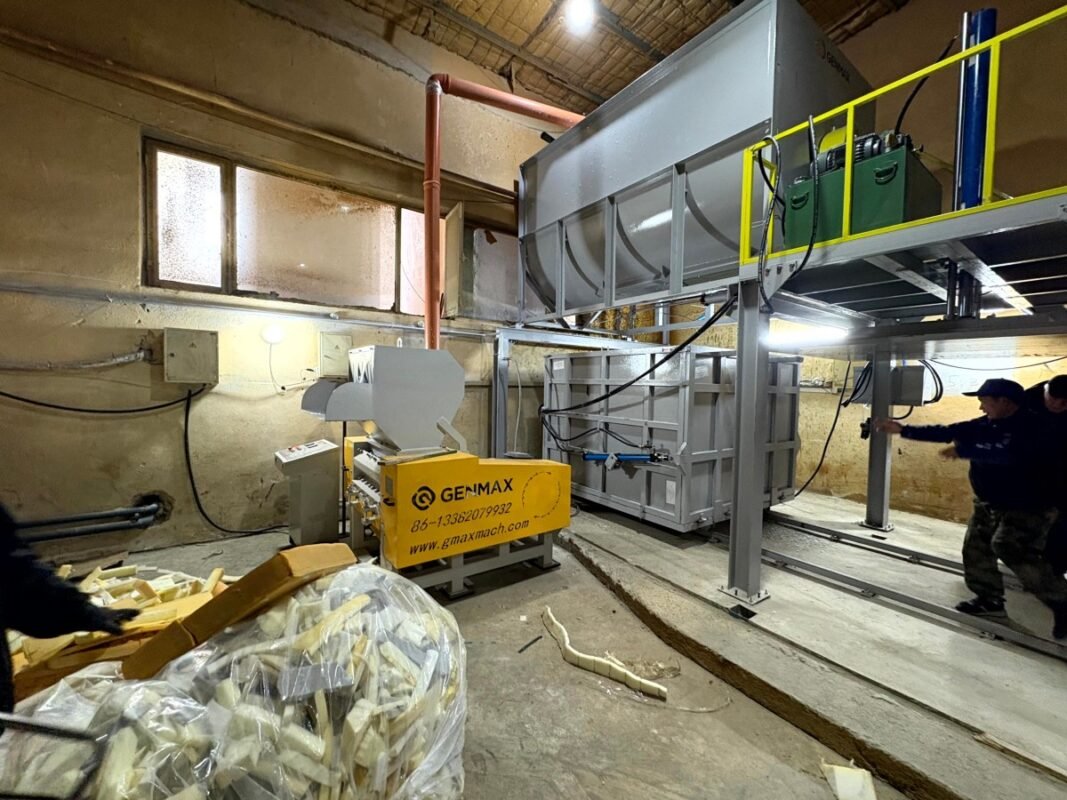
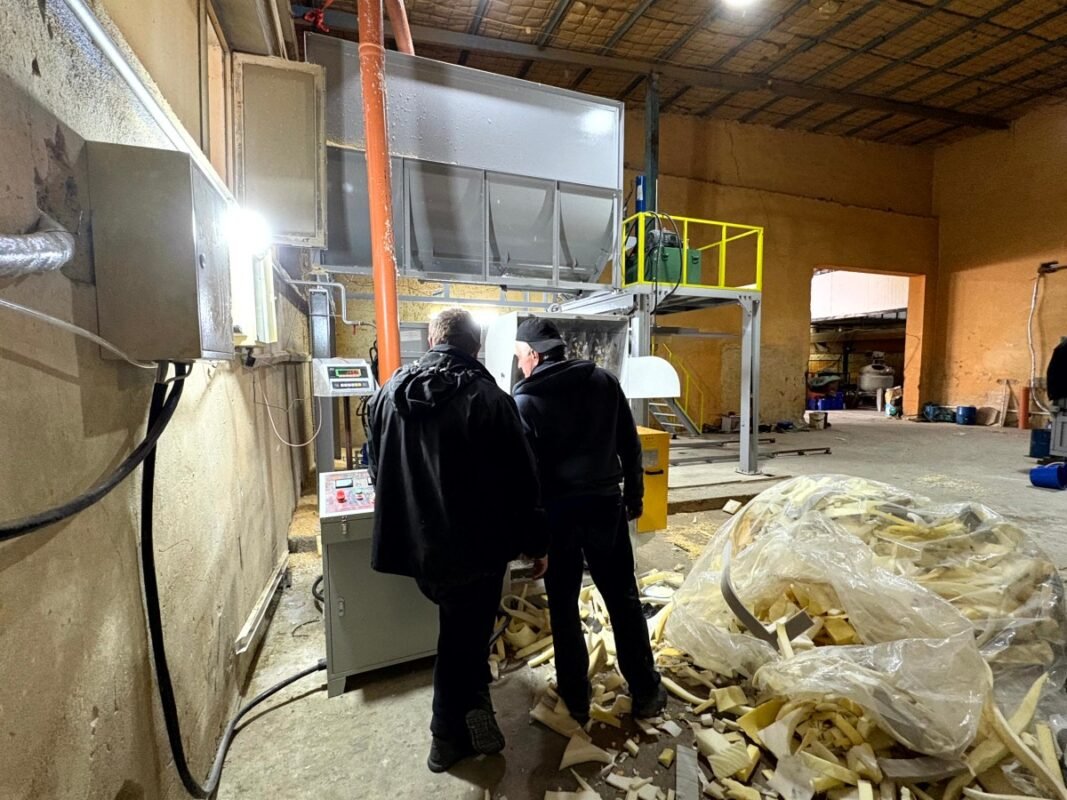
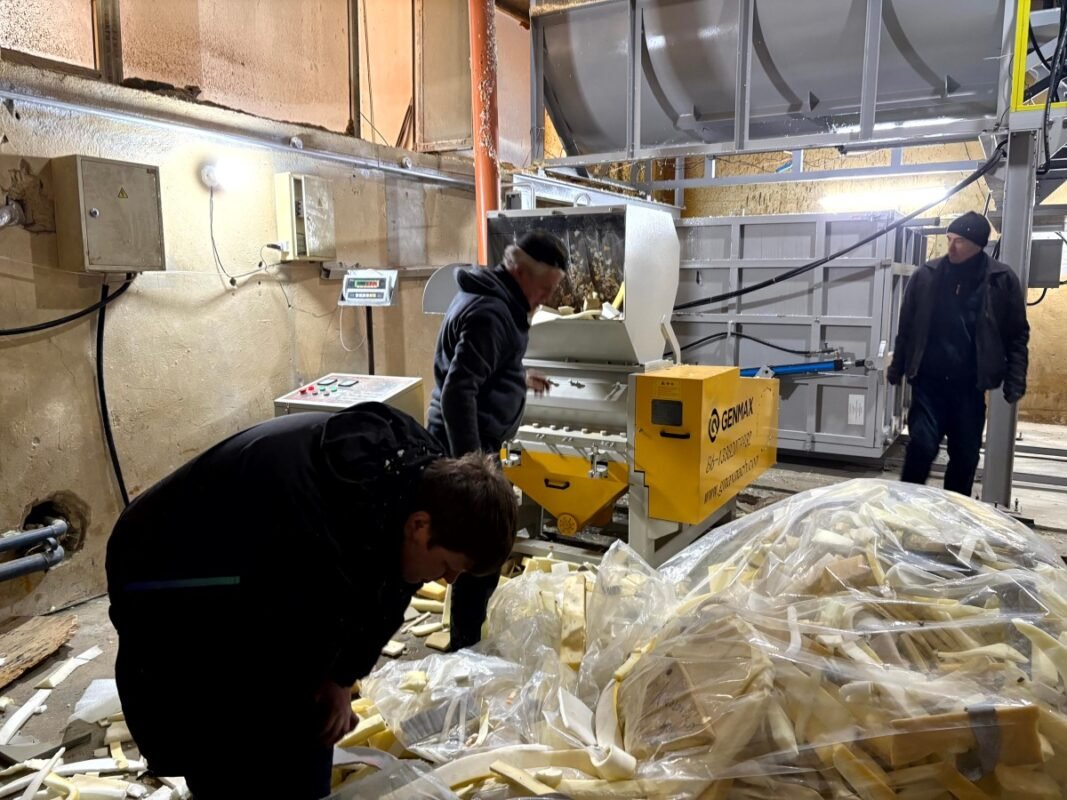
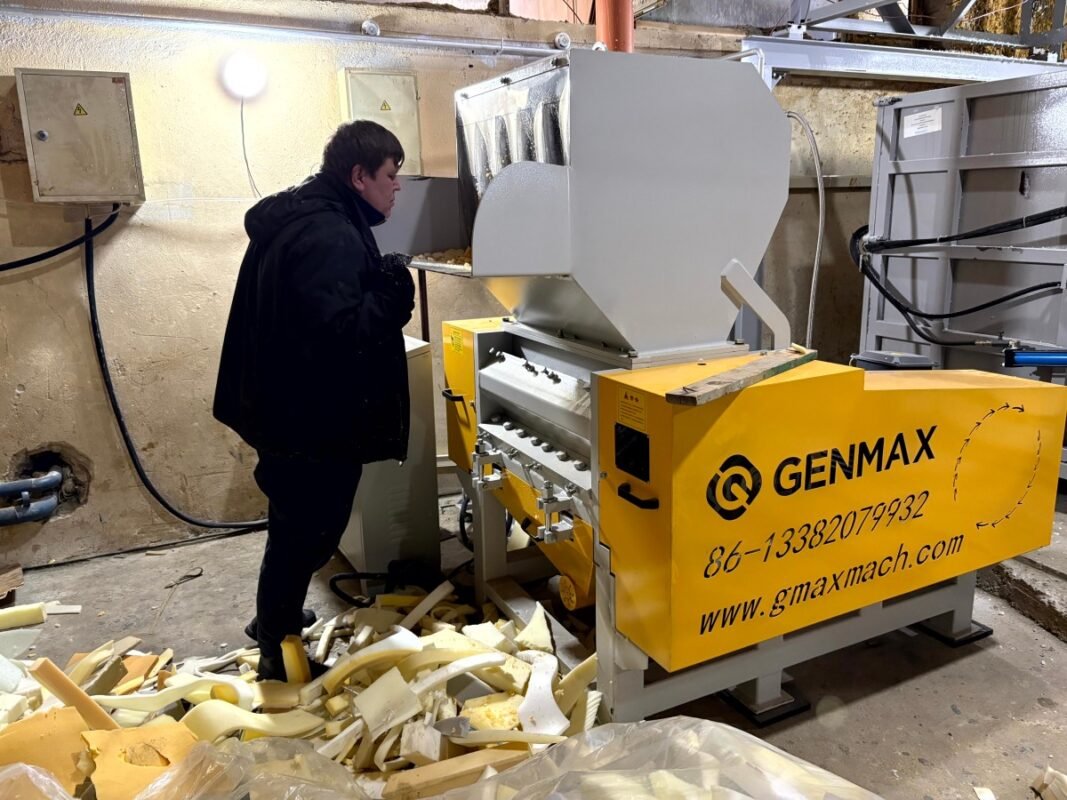
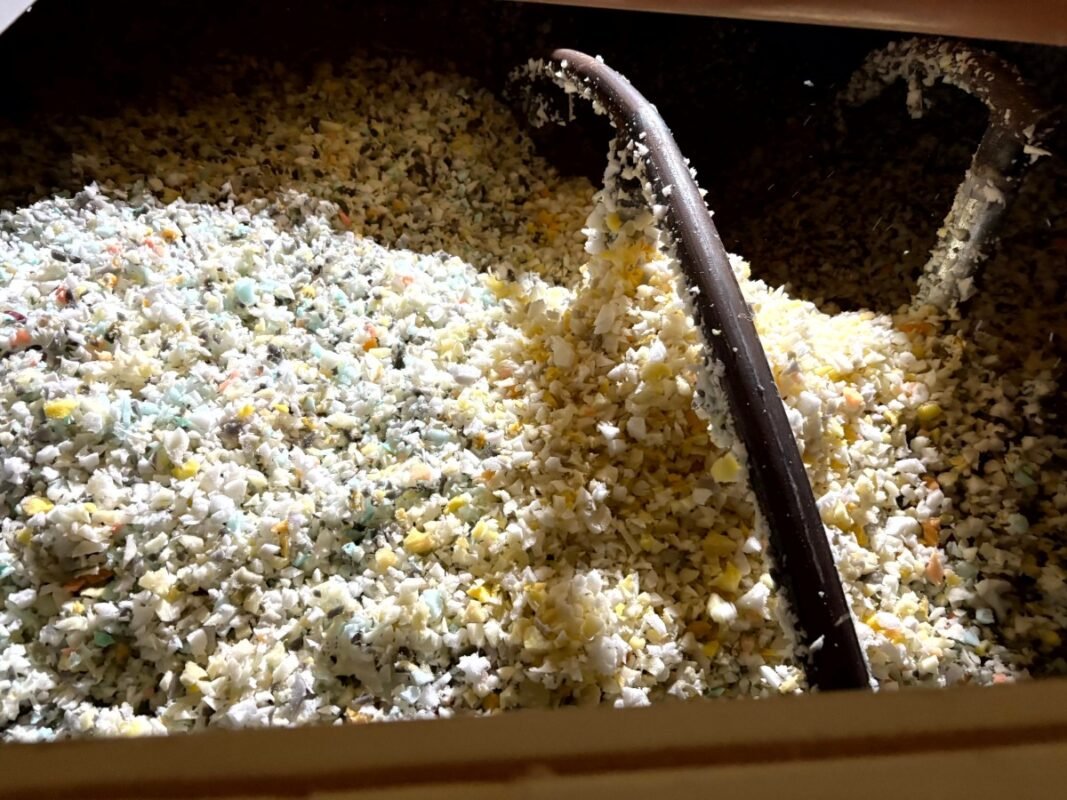
RF02 Foam Rebonding Machine with Steam
- Converts shredded foam scraps into strong rebonded foam blocks
- Produces both rectangular and cylindrical blocks for versatile applications
- Advanced agitation system prevents crystallization during processing
- Built-in weight display meters glue and steam with accuracy for consistent bonding
- Hot press technology applies exact pressure and temperature for durable blocks
- Weight box measurement guarantees consistent material dosing each cycle
How the Recycling Line Works in Practice
- Shredding: Foam scraps crushed into granules by the PS3878-PU machine
- Mixing: Granules blended with glue and chemicals in a mixing vessel
- Molding: Mixture poured into molds, pressed, and steamed in the RF02 machine
- Finishing: Blocks cooled, edges trimmed, then cut into sheets or custom shapes
This system transforms foam waste into top-notch rebonded foam blocks. These blocks are used for carpet underlay, gym mats, packaging, and acoustic panels. This process cuts down on waste and opens new revenue opportunities.
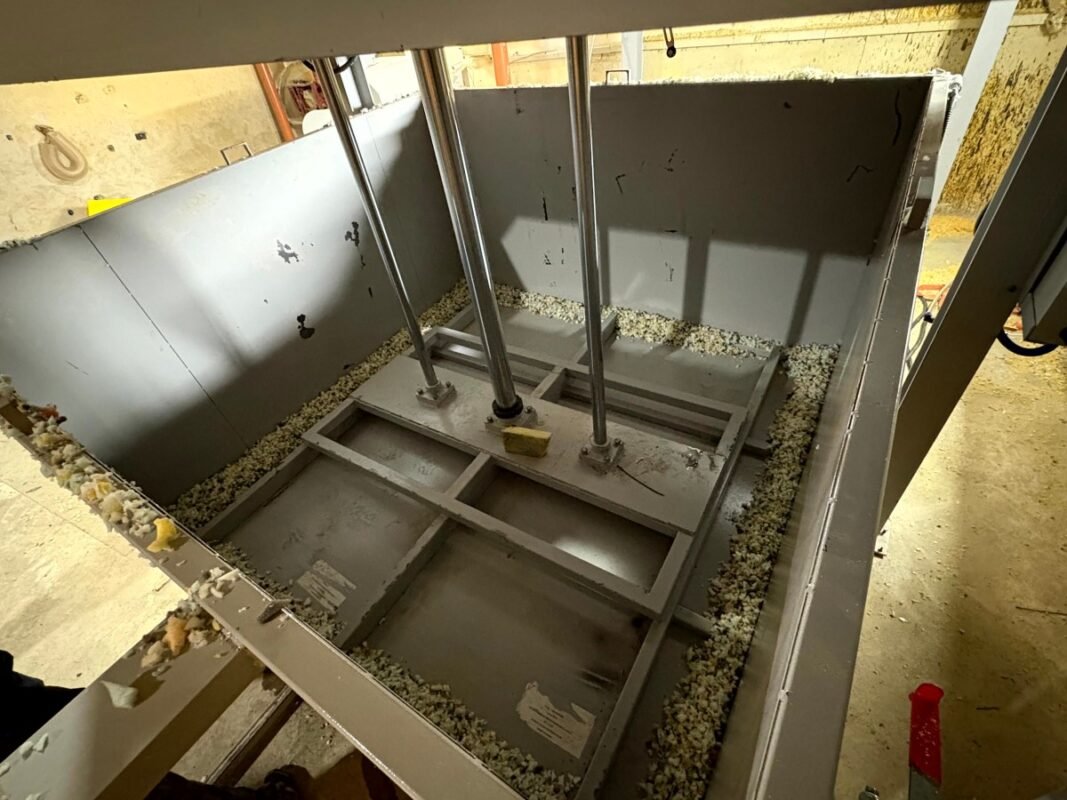
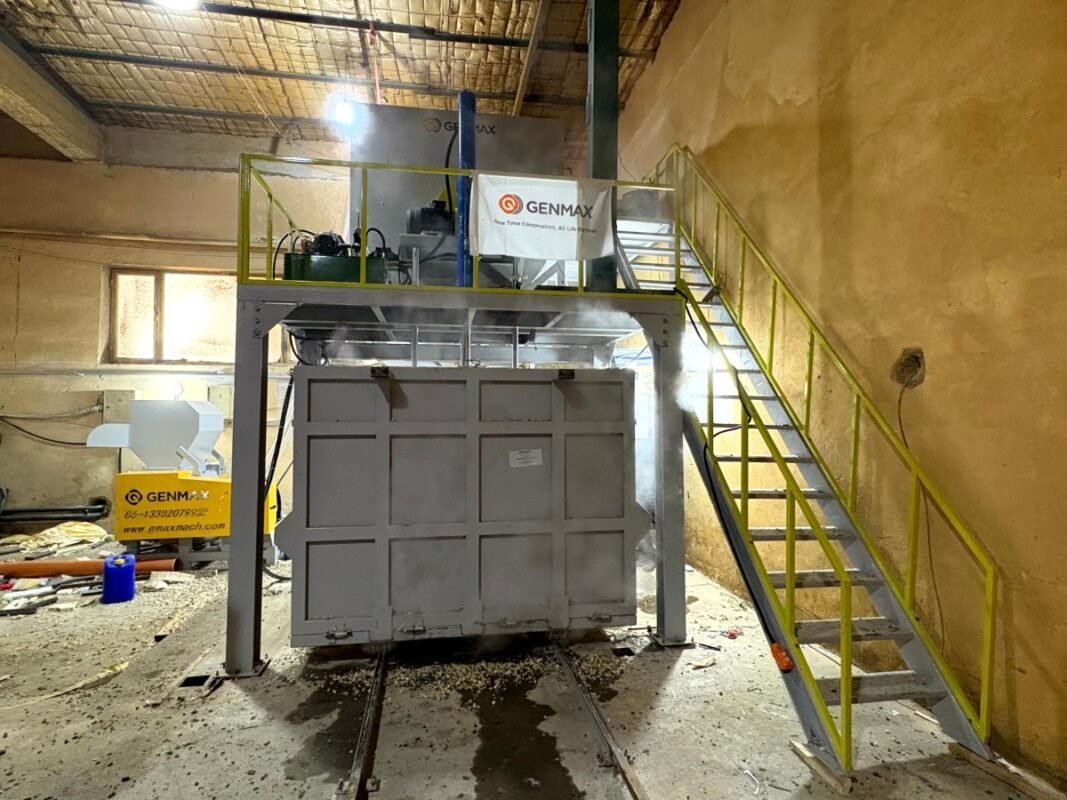
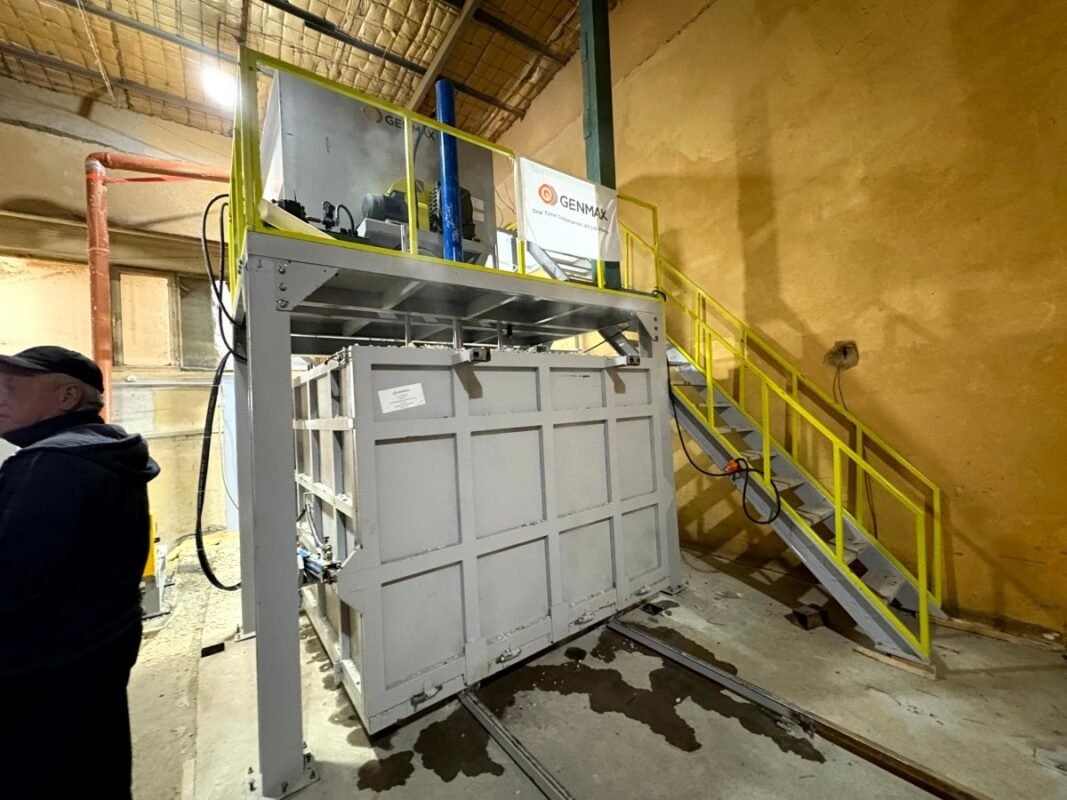
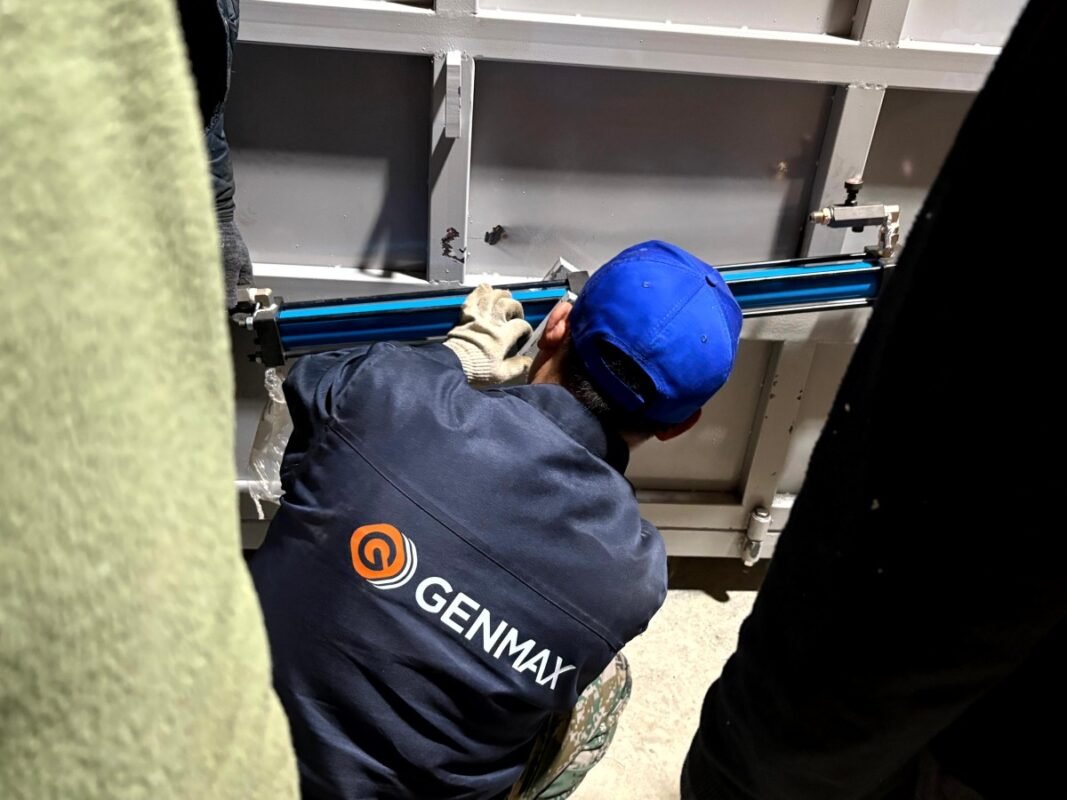
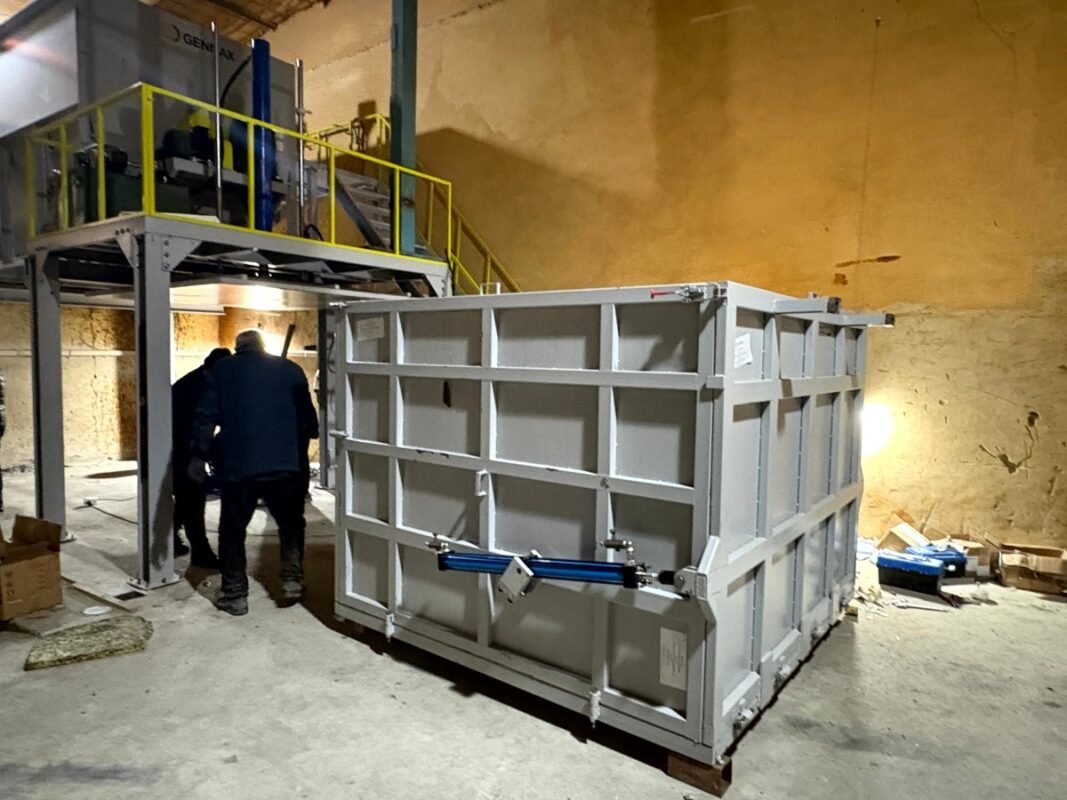
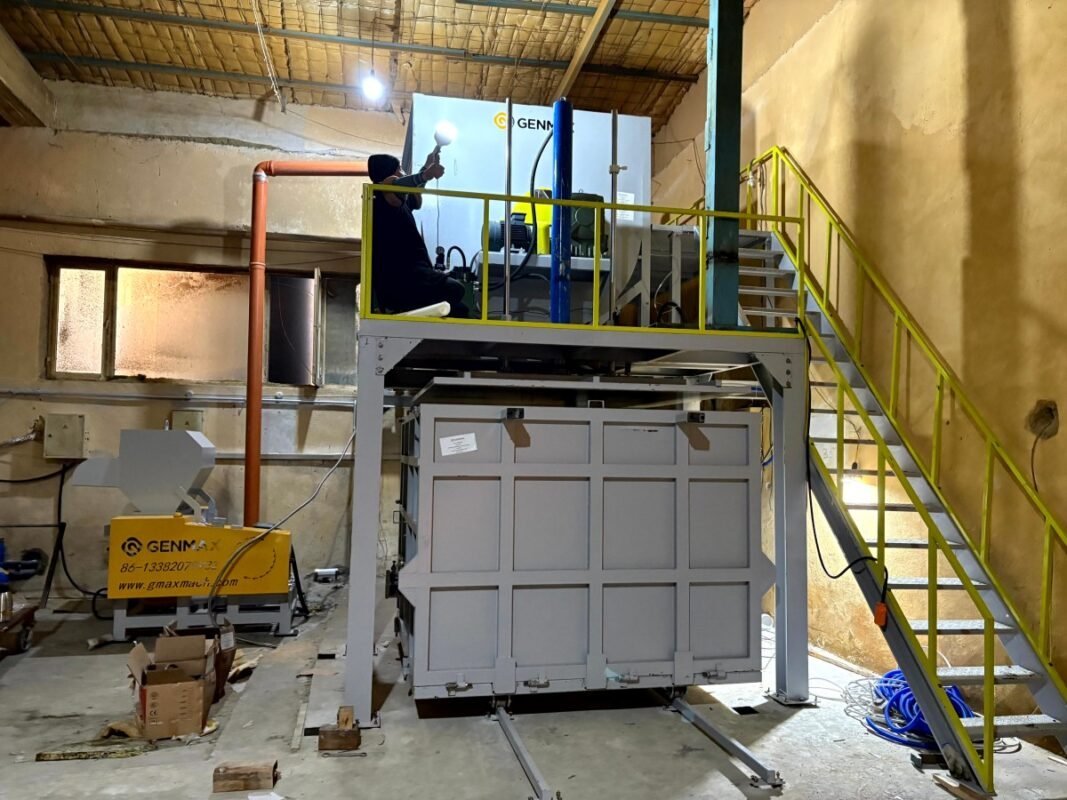
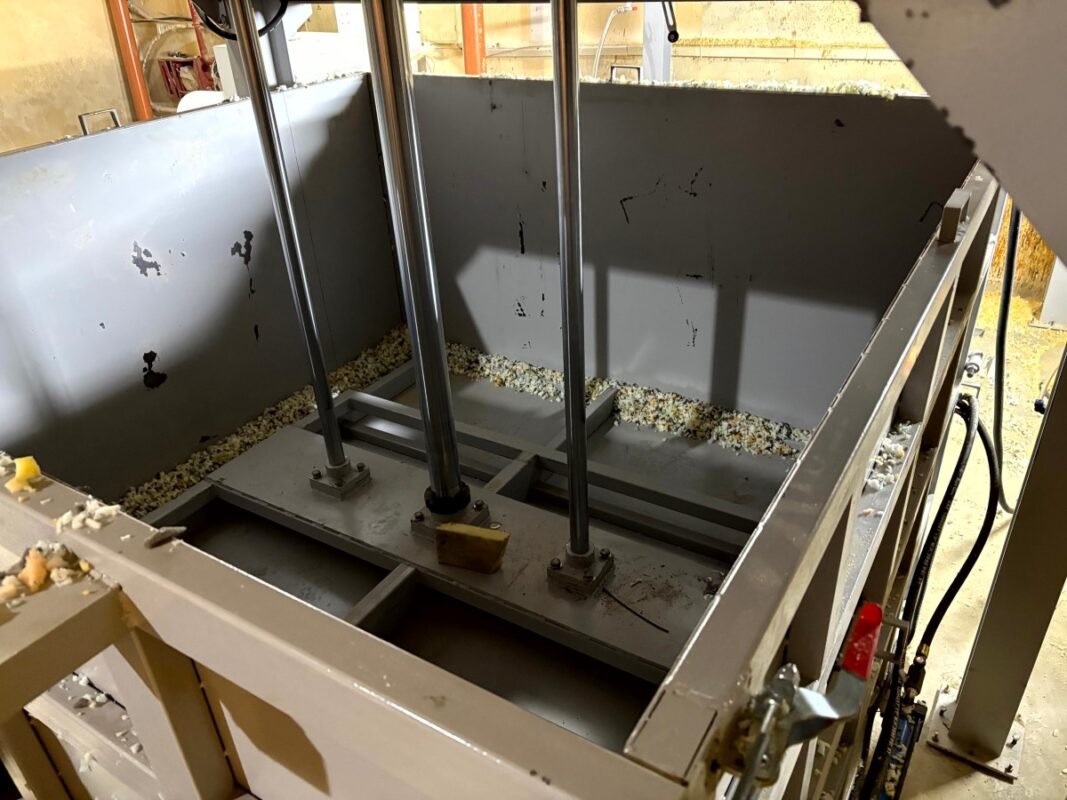
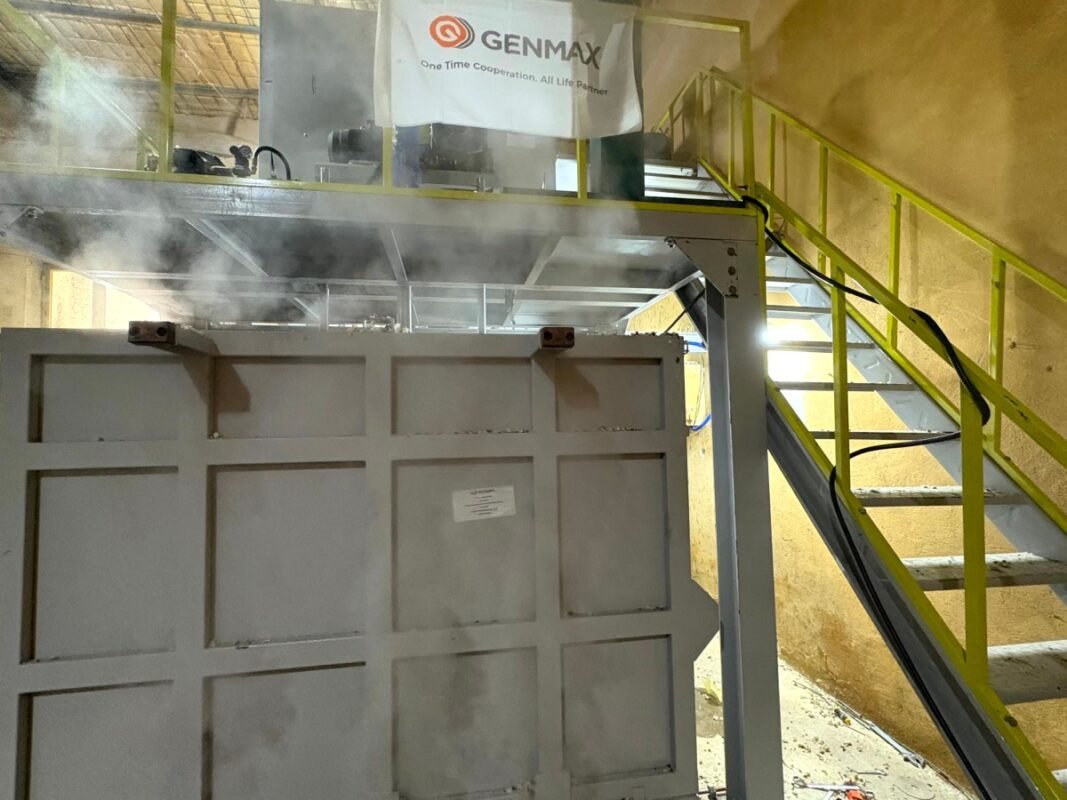
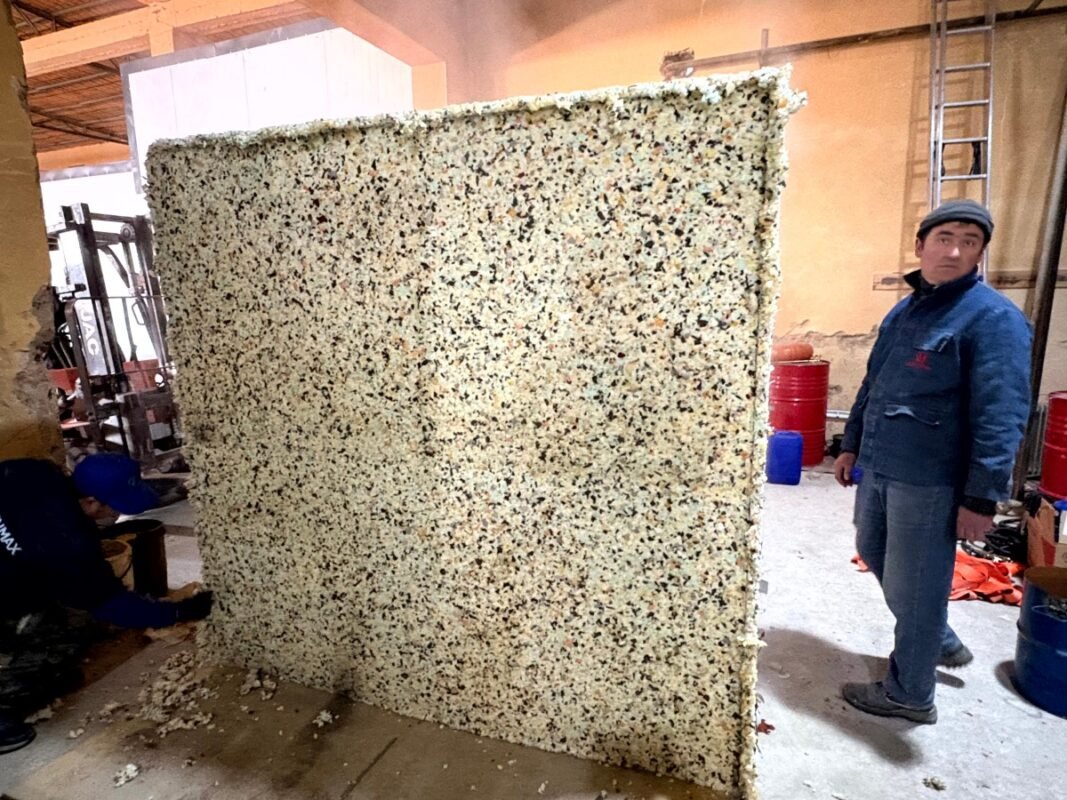
What GENMAX Brought to the Table
- Hands-on engineering: Our team managed installation, commissioning, and testing on-site. This ensured smooth operations right from day one.
- Custom-fit solutions: Machines tailored to handle the client’s specific foam scrap types and densities
- Sustainability gains: The factory reduced foam waste by 90%. This cut raw material costs significantly.
- Industry expertise: More than 15 years in mattress machinery and recycling tech. Completed over 5,000 successful projects worldwide.
- Full-cycle project management: We improved every step, from delivery to testing.
- Local support network: Service centers nearby and technical teams ready to assist whenever needed
What This Means for Your Factory
If foam scrap is piling up and driving up costs, consider these points:
- Invest in crushing and rebonding machines that fit your foam types and scrap amounts
- Use precise glue and steam control to produce consistent, durable rebonded foam blocks
- Choose suppliers who provide on-site support throughout installation and testing
- Manage your recycling line closely to maximize output and minimize downtime
- Embrace sustainability — recycling foam reduces waste disposal fees and cuts raw material purchases
Buying Smart: What Foam Recycling Factories Should Prioritize
- Capacity: Can the crusher keep up with your scrap volume without bottlenecks?
- Output quality: Does the rebonding machine make blocks that fit your product needs?
- Process control: Are glue and steam dosing systems accurate and adjustable?
- Support: Will engineers be on-site to ensure smooth startup and training?
- After-sales: Is local technical support available for quick troubleshooting?
Stay away from suppliers who only send machines. Recycling lines need expert setup and regular support to run well.
Performance Comparison: Traditional Foam Waste Handling vs. GENMAX Recycling Line
Feature | Traditional Handling (Discard/Sell) | GENMAX Recycling Line (Crusher + Rebonding Machine) |
Foam Waste Utilization | 0% (discarded or sold as scrap) | Up to 90% recycled into valuable foam products |
Environmental Impact | High waste, landfill or disposal | Significantly reduced waste and landfill use |
Revenue from Waste | Low or negative (disposal costs) | New revenue stream from recycled foam products |
Production Efficiency | No recycling process | Efficient crushing and rebonding for continuous use |
Cost Savings | None | Reduced raw foam purchase and waste disposal costs |
Sources
- United Nations Environment Programme, “Sustainable Foam Recycling Practices,” 2024 Report
- Uzbekistan Ministry of Industry and Trade, “Manufacturing Waste Reduction Initiative 2025”