Moroccan Manufacturer Explores GENMAX Foam Rebonding Solutions
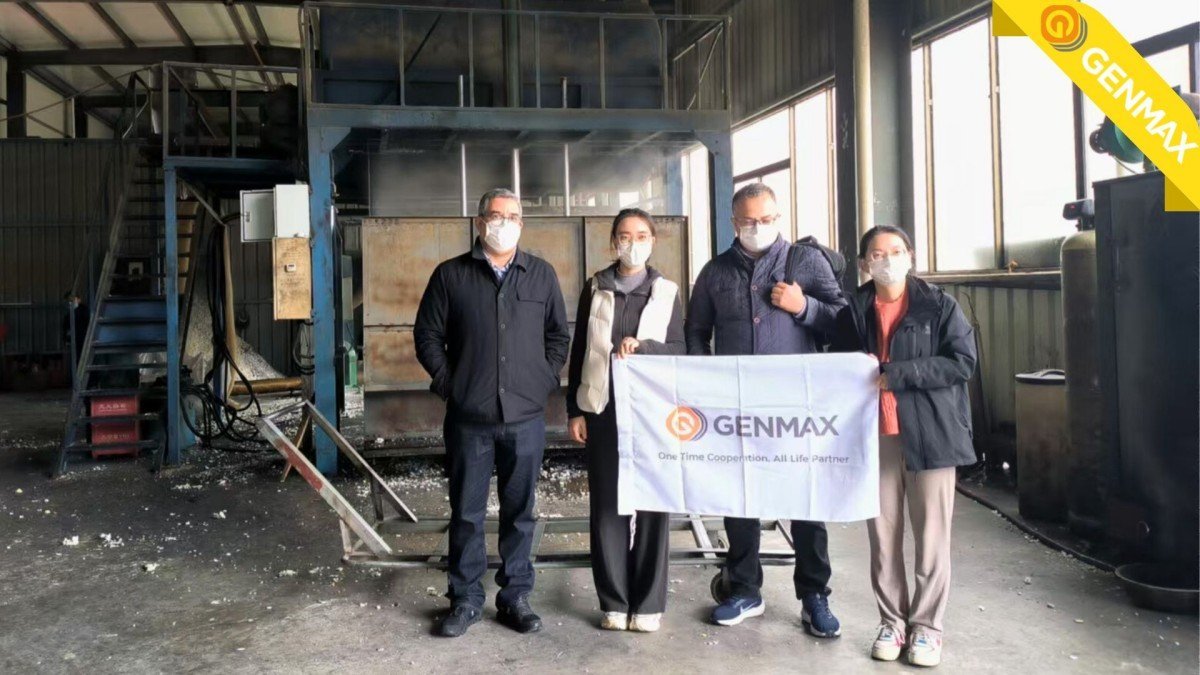
A manufacturing team from Casablanca visited our facility last week. They wanted to check our PU foam rebonding systems. Their goal is to turn foam waste into marketable products. This trend is growing across North Africa.
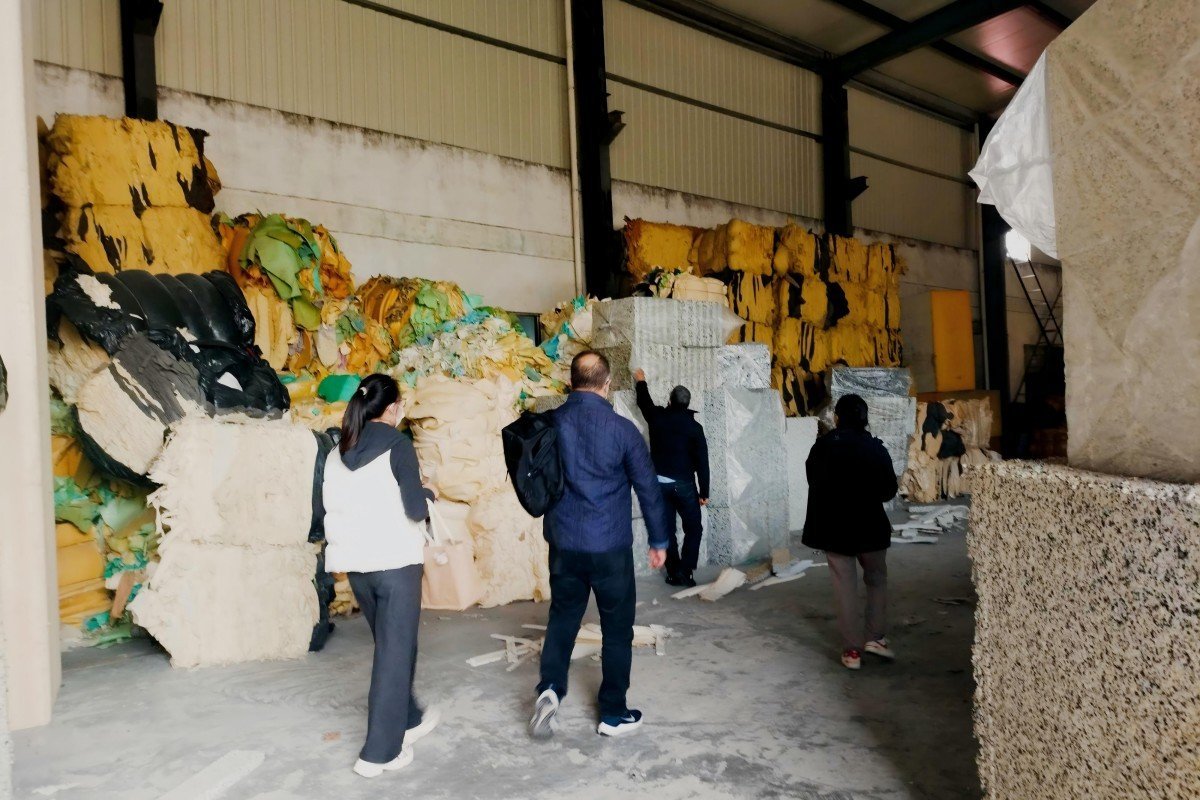
Textile industry representatives from Morocco examining compressed waste baled foam materials at the preprocessing stage of the foam recycling operation.
Turning Waste into Opportunity
“Foam scrap is too valuable to throw away,” the company’s technical manager said. Their current operation produces a lot of polyurethane waste that they want to reuse.
The Moroccan market is seeing more demand for rebonded foam products. These include sound insulation and flooring underlay in construction. The company plans to invest in new processing technology. They hope this will turn waste into a new source of revenue.
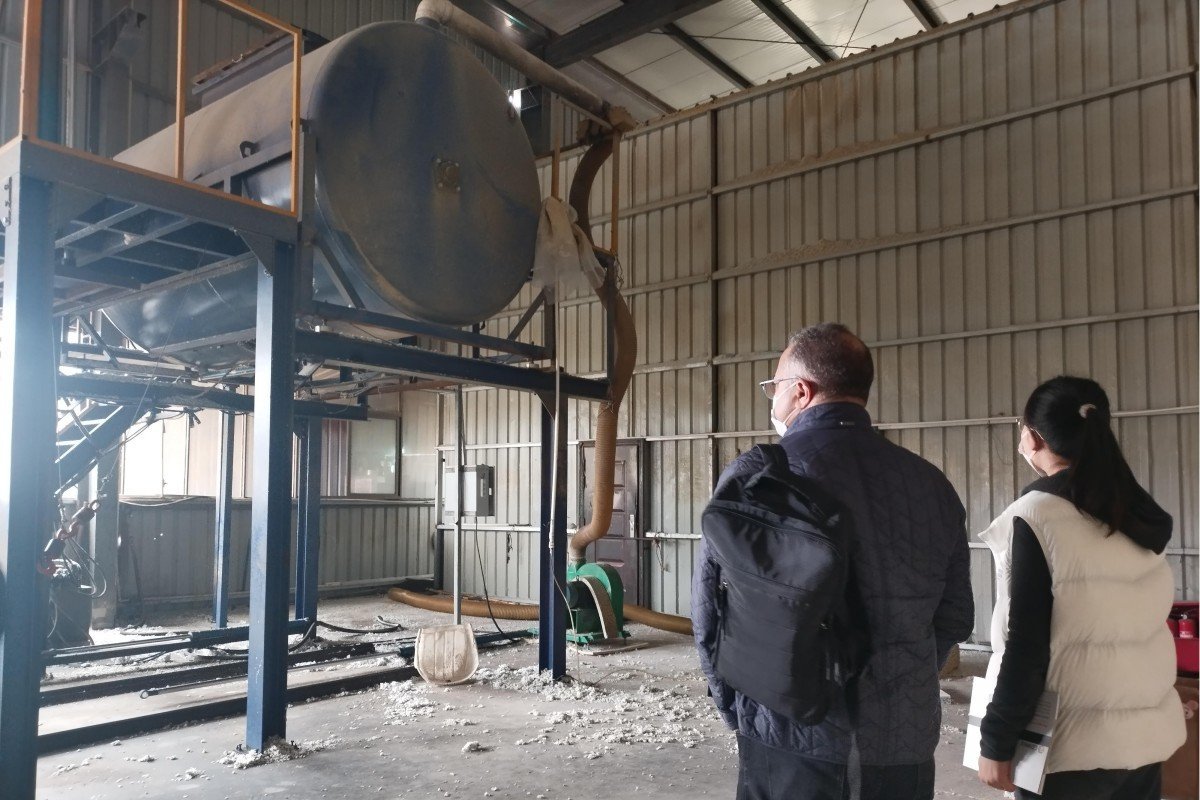
Technical specialists explaining the operational features of the foam rebonding equipment to Moroccan industrial customers interested in sustainable manufacturing solutions.
Practical Evaluation
I was impressed by their careful evaluation method. Instead of only looking at technical specs, they asked specific questions about:
- Processing capabilities for various types of foam scrap
- Output consistency and properties of the final product
- Production costs, including energy use and adhesive needs
- Maintenance needs and availability of spare parts
They tested density and compression strength of rebonded foam samples. These are key properties for their target applications.
“The consistency is critical,” noted their production lead. “We need to meet specific technical requirements to sell in the construction market.”
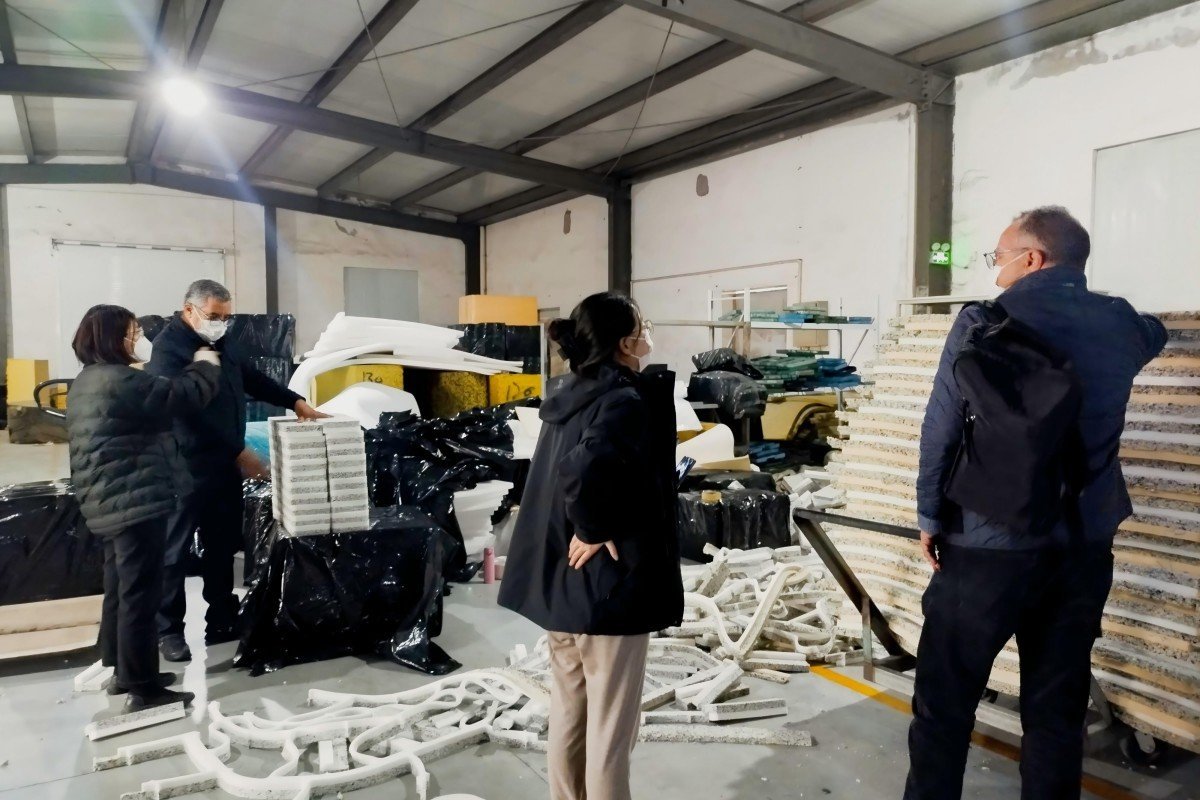
Moroccan industrial buyers carefully inspecting the quality of finished recycled foam products produced by the rebonding machine system during their factory assessment visit.
Economic Considerations
Their economic case clearly drove their interest. The team looked at waste disposal costs and checked selling prices for rebonded foam in Morocco.
When we discussed how our system’s density control could help them make higher-value products, they saw the potential. They could target premium applications instead of just competing on price in basic markets.
Local Implementation
Our talk naturally shifted to specific implementation challenges in Morocco. The team raised practical concerns about:
- Chemical supply chains in North Africa
- Training needs for their production staff
- Adapting to local power systems and operating conditions
These points show the real challenges of using new production technology in developing markets.
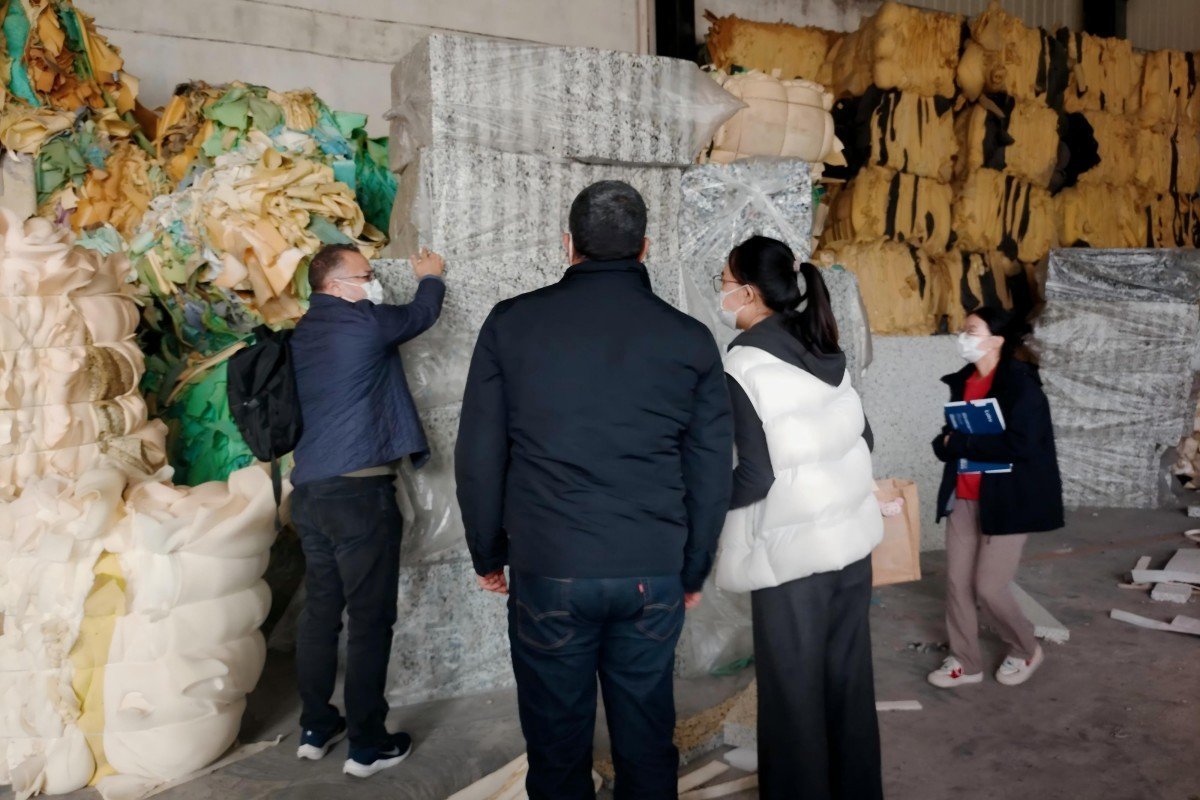
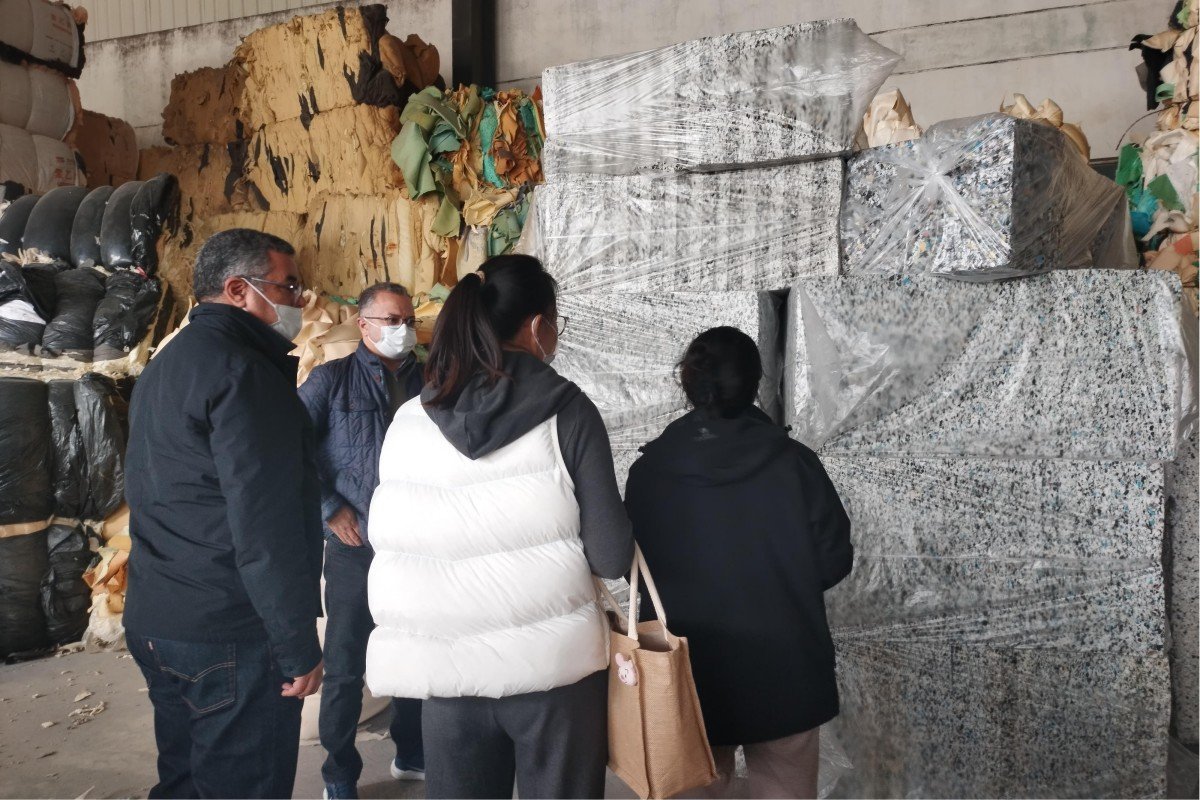
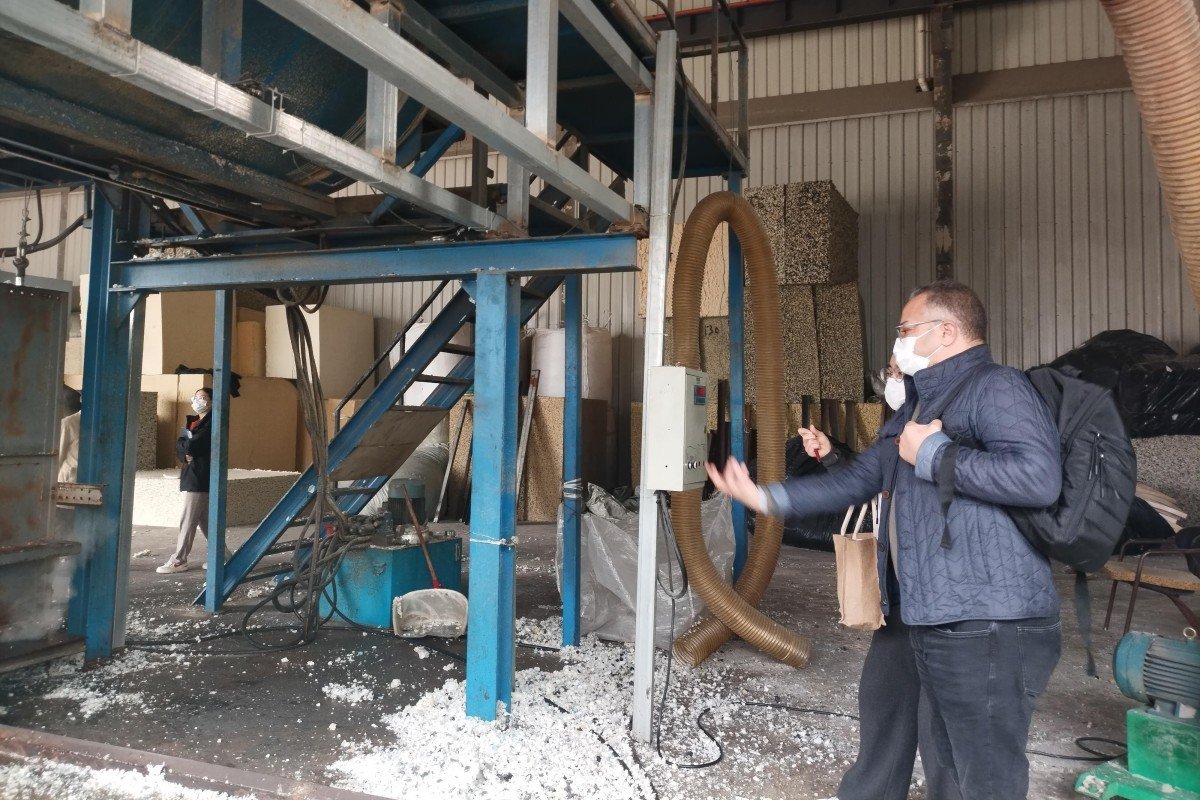
Next Steps
The Moroccan team is considering their choices. They are balancing quick waste reduction with long-term market chances. They plan to make a decision this quarter as part of their broader goals for manufacturing efficiency.
Their approach shows that manufacturers in emerging markets see sustainability as a business chance. They are turning environmental challenges into market opportunities.