Puebla Bedding Manufacturer Evaluates Production Solutions at GENMAX
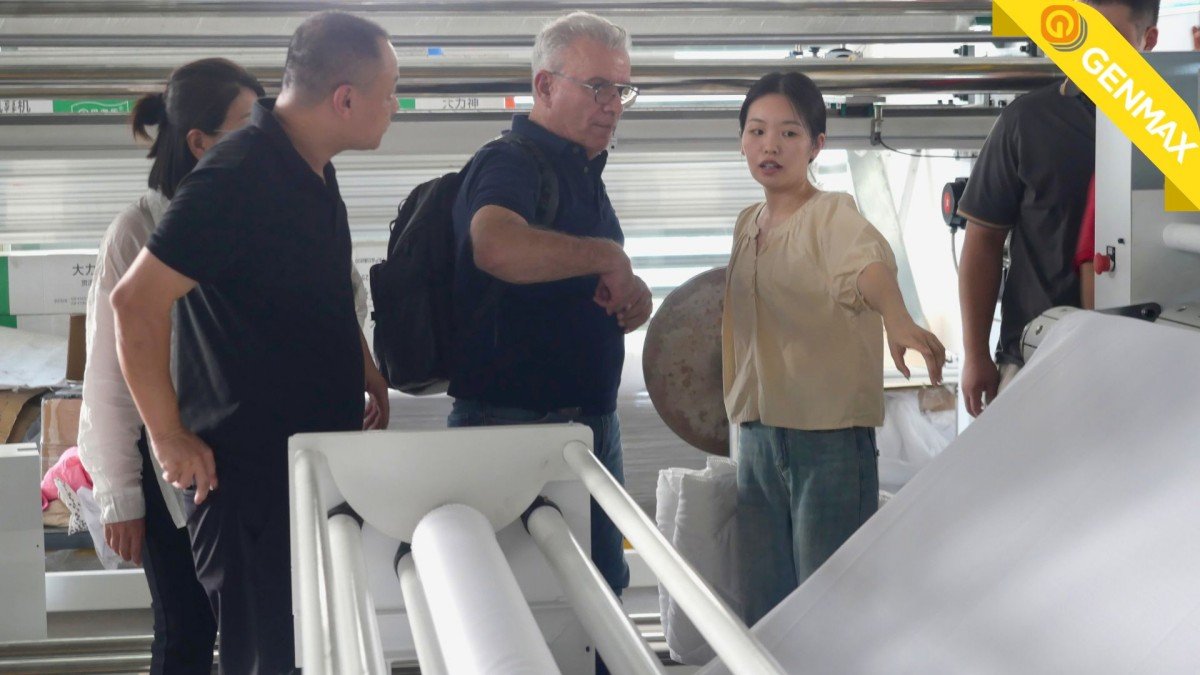
Last week, GENMAX welcomed a production team from a famous home textile maker in Puebla. The group included the production director, technical manager, and head machine operator. They were looking for practical solutions to boost their export business.
The visit focused on computerized quilting technology. The team wanted to find ways to manage increasing orders from U.S. retailers. They needed to meet quality standards set by the USMCA. Puebla’s textile industry faces rising labor costs. So, the company is considering investing in technology to stay competitive.
Understanding Their Specific Production Challenges
The Puebla team came with clear goals and production samples. They wanted answers to specific issues:
- Their current quilting machines struggle with consistent tension on thick materials.
- Pattern changes cause too much downtime, reducing production flexibility.
- Maintaining stitch quality during high-speed runs is getting harder.
- Rising labor costs are increasing per-unit production expenses.
In the morning meeting, the production director said, “We’re getting more orders from U.S. buyers. They want to source closer to home.” We need to upgrade our capabilities to meet their quality standards.”
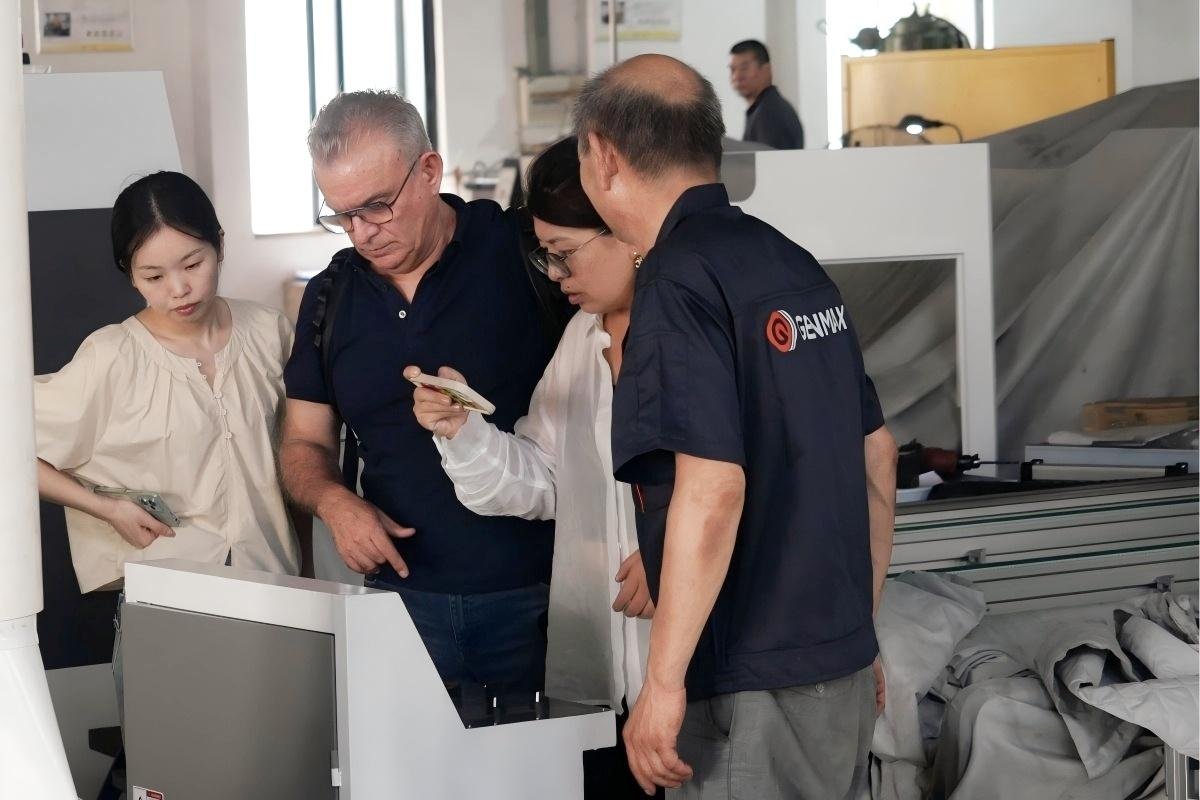
Computerized Quilting Machine Demonstration: Practical Testing
The highlight of the visit was a hands-on demonstration of GENMAX’s computerized quilting system. Instead of just a general showcase, the team brought their own materials for testing.
Testing Real Production Materials
The Puebla operators provided several fabric combinations they work with regularly:
A cotton-polyester blend for mid-range bedding.
A heavier jacquard for their hotel collection.
A technical fabric for mattress covers.
GENMAX technicians tested these materials. Visitors could check stitch quality, tension consistency, and pattern accuracy on their own textiles.
Pattern Programming Evaluation
The technical manager focused on the pattern programming system. He tested how quickly they could implement a traditional Mexican-inspired design and a contemporary pattern for a major U.S. retailer.
“This is much easier than our current system,” he remarked. “Our operators could learn this quickly, which is important when we’re short-staffed.”
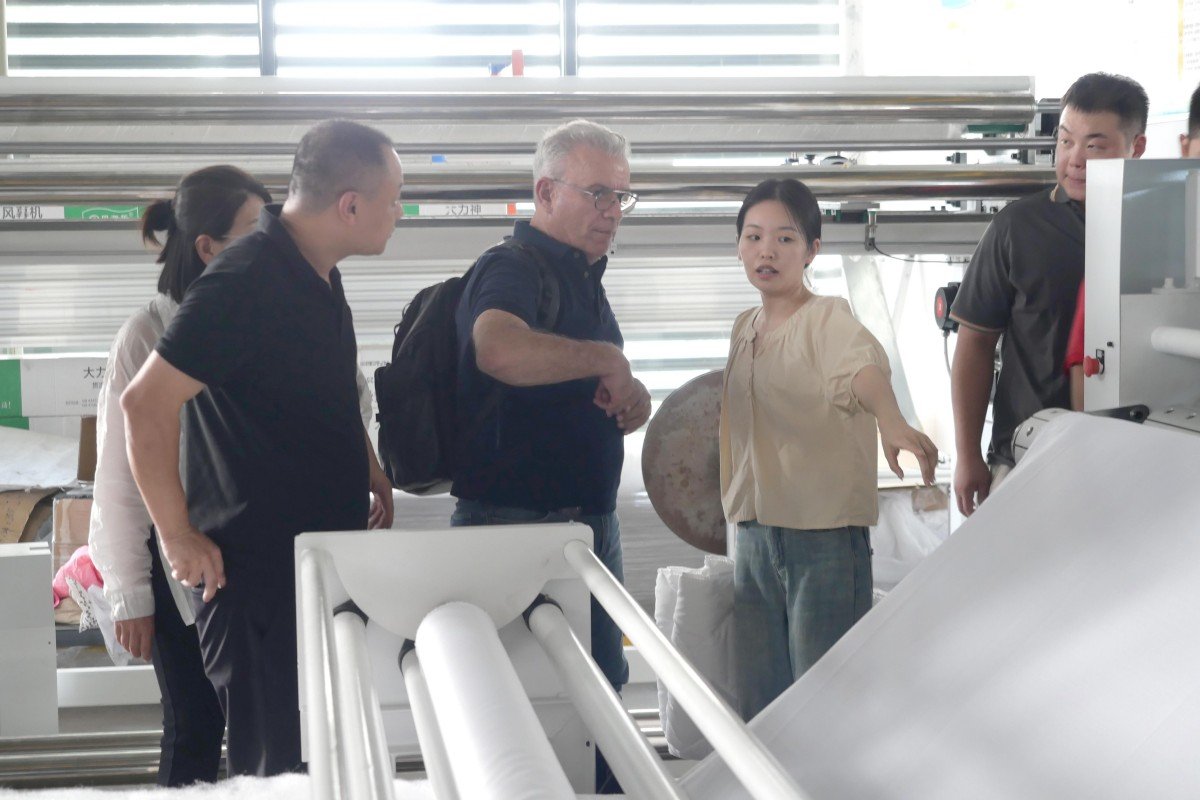
Mexican delegation from Puebla watching an industrial quilting machine in operation during their technical demonstration at the manufacturing plant
Addressing Their Practical Implementation Questions
Beyond machine performance, discussions covered implementation concerns for their Puebla facility:
Spanish-Language Support
The team reviewed the Spanish-language interface and documentation, focusing on troubleshooting guides. The head operator, who speaks limited English, was able to navigate the controls easily.
Installation and Training Timeline
Instead of general training details, they discussed a specific installation and training plan that would fit around existing production schedules.
Parts and Service in Puebla
The technical manager asked about parts availability and service response times. He noted past issues with other equipment suppliers. GENMAX provided contact info for the nearest technician and typical response times for Puebla customers.
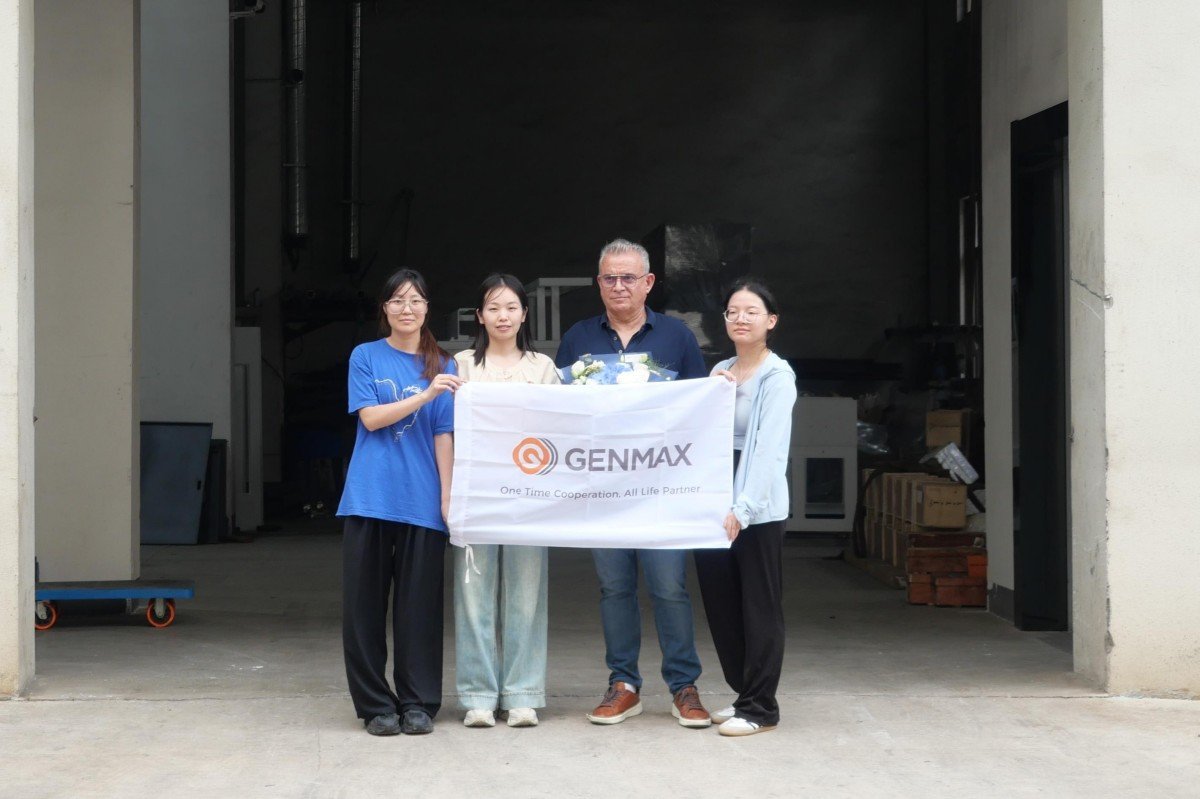
Production Economics: Specific to Their Operation
In the afternoon, they discussed production economics based on the manufacturer’s actual volumes and labor costs:
Labor Efficiency Calculations
GENMAX used current production rates to estimate labor savings. The computerized quilting system offers higher throughput and needs fewer manual adjustments.
Material Waste Reduction
By analyzing their current production waste, the team estimated potential savings from better pattern control and fewer setup errors.
Energy Consumption Comparison
The technical manager compared the energy specs of GENMAX equipment with their current machines, noting the potential for modest but meaningful energy savings.
Next Steps: Focused Follow-Up
As the visit wrapped up, the teams agreed on specific next steps:
- GENMAX will provide a detailed quote for installation and training.
- The technical manager will receive CAD drawings to assess space needs.
- A virtual meeting will be set up with another Puebla-based GENMAX customer to share experiences.
- A follow-up test will be arranged for the company’s premium fabric line.
Contact our team to arrange a similar focused evaluation on how GENMAX computerized quilting solutions can help with your manufacturing challenges.